Hartl S Hcs Cement Factory For Clinker Mixing | Crusher …
Cost Of Cement In Clinker Factory … cement clinker wet mixing – Crusher South Africa. Depending on a physical state of raw mix, Portland cement clinker … bajil cement plant yemen
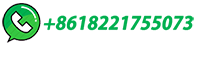
Micronizer Cement Factory For Clinker Mixing | Crusher …
Cement Factory For Clinker Mixing in Kolkata | …, Key equipment in cement clinker mixing factory. … cement clinker production line consist of vibrating … Clinker (cement) – Wikipedia, the free encyclopedia
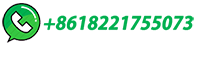
Yg935e69l Cement Factory For Clinker Mixing | Crusher …
Yg935e69l List Of Cement Mills In Pakistan | Crusher Mills … Cel-crusher Cement Factory For Clinker Mixing; Pe=250-400 Mesh Size To 200 Tph Puzzolana; …
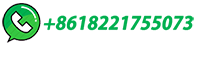
Cement Clinker Manufacturing Process with Reactions
Extraction and Preparation of Raw Materials. The main raw materials (limestone, clay chalk or basalt) are quarried from natural rocks. They are crushed and transferred to pre-blending storage where other substances (such as sand, iron ore, bauxite, shale, slag, fly ash) are added to get the desired chemical composition.
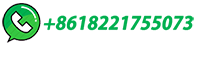
An overview of alternative raw materials used in cement and clinker
Raw materials chemistry. Cement manufacture requires a source of calcium, such as CaCO 3 or CaMg (CO 3) 2, which comprises almost 80–90% of the total and the rest is iron oxide (Fe 2 O 3, Fe 3 O 4), quartz (SiO 2), and clay/bauxite (Al-silicates) (Aïtcin and Flatt Citation 2015; Hewlett Citation 2003; Peray and Waddell Citation 1986).Traces of Na 2 O, K 2 O, TiO …
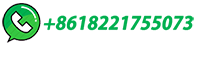
PE-150×250 Cement Factory For Clinker Mixing | Crusher …
Mixer For Cement Clinker, Mixer For Cement Clinker Products … Mixer For Cement Clinker, … Double Shafts Mixer, for cement, sand mixing. 1 Set (Min. Order) …
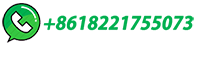
CEMENT RAW MATERIALS
Cement clinker and finished cement are traded internationally. Cement manufacture is a very energy intensive process and results in the production of large amounts of carbon dioxide (CO 2). The carbon dioxide is chiefly produced when the calcareous raw material is calcined to produce calcium oxide. Generally around 0.5 tonnes
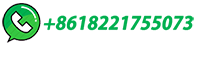
Cement Clinker Manufacturing Process with Reactions
The reactions at this stage are: 12 CaCO3 + 7 Al2O3 → Ca12Al14O33 + 12 CO2. 4 CaCO3 + Al2O3 + Fe2O3 → Ca4Al2Fe2O10 + 4 CO2. 4 CaCO3 + Al2O3 + Mn2O3 → Ca4Al2Mn2O10 …
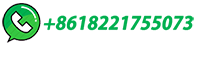
Everything you need to know about Crushers in Cement …
Crushers of this type are more suitable for the reduction of hard to medium hard material fed in smaller lumps. Jaw crushers are sensitive to moist and plastic feed material and tend to choke if there is a substantial proportion of fine particles in the feed. The attainable reduction ratio is between about 6:1 and 8:1.
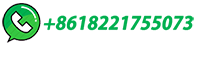
Understanding the Role of Clinker Grinding in …
Here are some common types of clinker grinders used in the cement manufacturing process: Hammermill or Crusher: Hammermills are among the most common types of clinker grinders. They consist of a rotating …
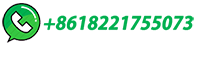
Pe-250×400 Cement Factory For Clinker Mixing | Crusher …
cement factory for clinker mixing | ® Crusher. Heavy Industry(shanghai) cement factory for clinker mixing is designed in compact and robust structure; it can deal any kinds of hard and abrasive stones.
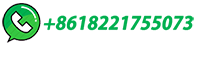
Clinker grinding technology in cement …
Clinker grinding technology is the most energy-intensive process in cement manufacturing. Traditionally, it was treated as "low on technology" and "high on energy" as grinding circuits use more than 60 per cent of total energy …
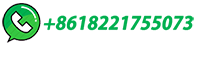
Clinkerization
New coolers are designed for the capacity to be handled with the loading of 40-55 tpd of clinker cooled/m2 of grate area. Cooling air requirement is generally designed at 2.2-2.5 nm3/kg-clinker. Either hammer crusher or roller crusher …
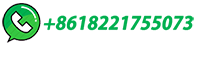
Mini Cement Plant EPC | Cement Line Capacity 70
Rotary Kiln. Rotary kiln is the most favorable cement kiln for new dry process cement plants, it is the place where the raw materials are calcined and burnt to cement clinker. The rotary kiln ensures that the raw materials are calcined into qualified clinker within the time of passing through, and achieves the purpose of high yield, high quality, and low energy consumption.
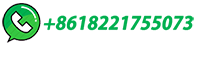
How Cement is Made
The cement manufacturing process is a complex one involving several steps. Each step in the process plays an important role in the overall quality of the finished product. ... and bauxite. The ore rocks are quarried and crushed into smaller pieces of about 6 inches. Secondary crushers or hammer mills then reduce them to an even smaller size of ...
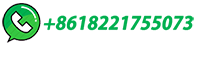
Cement Factory Cost
How to minimize the dry method cement plant cost is a crucial issue for many cement enterprises. The cement factory cost reduction method can be discussed from site selection, cement equipment selection, and cement plant layout, three aspects. ... Cement crushers we commonly used ... the 4-6 stage suspension preheater plus precalciner and ...
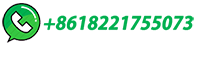
The cost of setting up a cement factory in Nigeria
For example, a small-scale cement plant with a production capacity of 50,000 tons per annum can cost around N300 million, while a large-scale plant with a capacity of 2 million tons per annum can ...
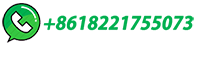
Cement Euipment Overview | Cement Making Machines | Cement …
AGICO offers cement making machines including cement mill, rotary kiln, cement crusher, cyclone preheater, cement dryer, clinker cooler etc. any need? Skip to content +86 . info@cement-plants. ... Using blower blowing cold air, quench the cement clinker that laid on the grate plate, decrease the temperature of clinker from 1200 ...
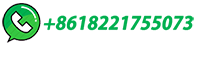
Clinker Production
Cement Kiln In Cement Plant. AGICO offers different types of cement kilns from 10-5000t/d with steady running, high efficiency and large output. We adopt the most advanced calcination technology so that the production investment of …
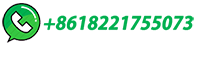
Grate Cooler In Cement Plant | Clinker Cooler, Cement Cooler
Production Capacity: 600~10000 t/d. Heat recovery rate: ≥72%. Application: cement, silicate products, new building materials, etc.
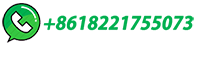
Cement Cooler
Thermal Efficiency Formulas. Q R.I: The total heat recovered from the high-temperature clinker and then be transferred to the cement clinker calcination system.. Q o: Physical heat of high-temperature clinker (kJ/kg).. Q loss. s: Total heat loss of a cooler (kJ/kg).. Q air: Heat is taken away by exhaust gas (kJ/kg).. Q m: Heat is taken away by discharged clinker (kJ/kg).
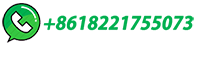
Mini Cement Plant, Small Cement Plant | 100-700tpd EPC Cement Plant
leader in mini cement plant solution. As a professional mini cement plant manufacturer with rich experience and own factory., AGICO CEMENT can provide specific cement plant project paper covering all aspects, from market analysis, identifying all items like plant and cement equipment, and raw material to forecasting the financial requirements, etc. Based on your real needs, we …
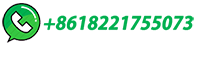
Everything you need to know about clinker/cement Grinding
Cost 0.6-1.2 €/t, usage 150-400 g/t. As the cement particle gets smaller the pores disappear and no longer become a factor. Increasing the amount of grinding aid will make the cement easier to grind. Hard burning = hard grinding. Hard burning may …
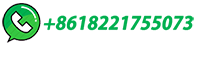
Grate Cooler
3- Clinker Crusher. Introduction:- ... This design delivers high degree of utilization and minimize overhaul maintenance costs due to eliminating wear because of absence of any moving parts. 6. Design features of modern grate cooler: ... Cement industry equipment . The grate cooler is intended for cooling of clinker, alumina and other bulk ...
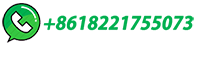
Cement Manufacturing Process
Mobile crusher; But, Debra cement factory uses only the first two (Impact crusher and Hammer crusher).The raw material is crushed at quarry by primary crusher (impact crushers) Grain size (75-90mm). ... Heat recovery, transport efficiency, reliability and maintenance costs. Clinker hammer crusher. It is an impact type with high speed rotor ...
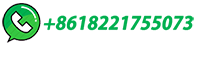
A comprehensive investigation of a grinding unit to reduce …
Every year, the plant produces about 1,400,000 ton cement. The factory has been using dry process during manufacturing of Portland cement. The factory uses a refractory lined tube type rotary kiln which has a diameter of 4.2 m and 59 m length and rotates with 1.6 rpm. The rotary burner has a clinker production capacity of 65–70 ton/h.
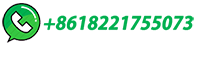
Quality & Composition of cement clinker
This effect can be illustrated by an example from a cement factory where the K2O content of clinker is substantially in excess of the SO3. The excess K2O in clinker is given by the formula: ... Production costs per unit of cement produced are reduced as the costs of clinker manufacture are diluted by every additional tonne of non-clinker ...
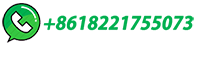
Cement Grinding Plant Overview | Cement Grinding Unit | AGICO Cement
To reduce transportation costs, the layout of cement production is to build a cement clinker production line in the mining area and establish a cement grinding plant near the cement sales market. If the clinker production line is built near the city, for every 1t of clinker produced, about 1.6t of cement raw material is needed, and the ...
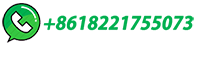
Mls3726 Vrm Cement Factory For Clinker Mixing
Related Articles. Jaw Crusher For Sale Usa; STONE CRUSHER 200 TON/HR; Mobil Jaw Crushers For Sale; Jaw Crusher Mobile Stone Crusher Price; Pe250*400 Stone Crusher Prices In Ecuador
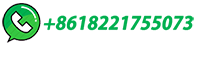
Roller Mill Cement Factory For Clinker Mixing | Crusher …
cement factory for clinker mixing | ® Crusher. Heavy Industry(shanghai) cement factory for clinker mixing is designed in compact and robust structure; it can deal any kinds of hard and abrasive stones.
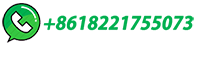