Latest Advances in High Capacity, Fine Screening for the Iron …
Efficient, reliable, high-capacity screening machines can increase recovery of fine iron ore and produce high-grade iron ore products. 's decades of …
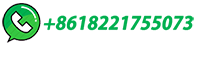
What are the definitions of a wet metric ton and a dry …
A wet metric ton and a dry metric ton are terms commonly used in the mining and shipping industries to measure the quantity of materials, particularly minerals like iron ore.
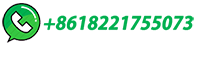
Differences between Dry Magnetic Separator and Wet …
They are generally used for selecting fine strong magnetic ore, weak magnetic ore, and iron powder. Ⅲ. Differences between dry and wet magnetic separators (1) Different feeding. Dry magnetic separators can separate the ore whose humidity is below 5%, and the beneficiation process of wet magnetic separators must rely on water as the medium.
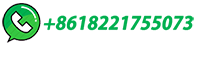
For dry and wet processing Low Intensity Magnetic …
The dry models are intended predominantly for material 2 to 200 mm in dry or nearly dry state like crushed iron ore. The wet models are designed for material of a few micrometres size to
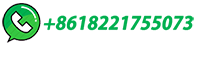
Intelligent dry fog dust suppression system: an efficient
An intelligent dry fog dust suppression system has been developed to control dust emission from mining and mineral processing activities. The developed smart dry fog dust suppression system was installed in a crushing and screening plant of an iron ore mine, and its performance was evaluated.
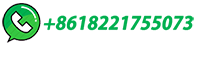
Dry Drum Magnetic Separators
Through different magnetic circuit designs and rotation speed options, our dry drum magnetic separators deliver high grade concentrate, middlings and tailings quantities. Our Dry Drum Magnetic Separators features: Ideal for cobbing iron ore beneficiation or banded iron stone removal on a diamond plant
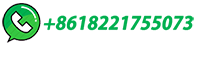
wet process for iron ore
Jan 07, 2017· iron ore wet processing plant, Iron ore processing Schenck Process Products:, Get Price the use of vibrating screen in iron ore washing .
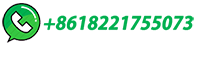
Characterization and Beneficiation of Dry Iron Ore
Characterization and beneficiation of dry iron ore processing plant reject fines of Khondbond region, India, was investigated. ... terization results, two process flow sheets comprising wet screening followed by conventional gravity concentration and two
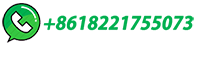
Principles of Screening and Sizing
(Wet, dry, slivers, openings) • Screen set-up • Speed, stroke, slope, direction of rotation, etc. • Feed rate (stph) and material bed depth • Media • Media type, open area, wire diameter, opening shape Information Required to Measure Screen ... Wet screening – Increases capacity ...
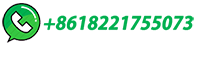
Wet Vs Dry Screening Iron Orewet Vsdry Processing Iron Ore
Wet Vs Dry Screening Iron Orewet Vsdry Processing Iron Ore. Wet Vs Dry Screening Iron Ore. Poor efficiency and major losses may be indicative of low probability during the screening process. 2.5 Dry Screening vs Wet Screening Dry screening refers to when a dry feed is fed onto a classifying screen.
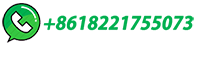
The six main steps of iron ore processing
When iron ore is extracted from a mine, it must undergo several processing stages. Six steps to process iron ore. 1. Screening We recommend that you begin by screening the iron ore to separate fine particles below the crusher's CSS before the crushing stage.
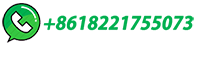
grinding by wet vs dry in iron ore – Grinding Mill China
cost of grinding by wet vs dry in iron ore. CEMTEC – Wet and Dry Grinding Technologies for Bulk Materials … Rotary scrubbers for iron ore beneficiation plants … With this pilot test plant CEMTEC is able … » More detailed. wet grinding vs dry grinding in ore concentrate. Wet vs Dry Grinding – bulk-online Forums. … is used to grind ...
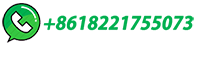
Dry Grinding VS Wet Grinding
The choice between wet and dry milling is, in general, unimportant in small-scale milling but is a major technical problem when large-scale milling in the metallurgical industries is involved. On purely mechanical grounds it is difficult to see any great difference in fundamental principles between wet and dry milling, since dry milling may be …
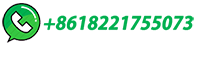
Grinding By Wet Vs Dry In Iron Ore
wet v s dry screening iron ore - vhgvoetbalpoule.nl. Cost of grinding by wet vs dry in iron ore while the hpgrs are a dry grinding system, isamill is a wet grinding process or finish grinding are on the iron ore, iron ore concentrate and gold ore sectors pared to the costs of a wet plant, the savings can am.
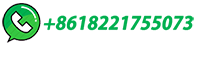
wet iron ore screening
The Latest Developments in Iron Ore Processing Mintekwet v s dry screening iron ore bondhumahalin. Process 600t/h lumpy iron ore • DMS Cyclone Only 6mm material for iron ore 360mm diameter cyclone Process 40t/h per cyclone • Larcodems 90 6mm stones 12m diameter Operating capacity of 600 800t/h Efficient separation at SG's as high as 41g ...
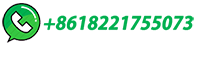
Wet High Intensity Magnetic Separators | Multotec
Wet High Intensity Magnetic Separators (WHIMS) from Multotec apply magnetism, matrix rotation and gravity to achieve para-magnetic materials separation. Applications include heavy minerals, ilmenite, manganese and iron ore (haematite) beneficiation; PGM upgrading as well as manganese recovery from slimes dams.
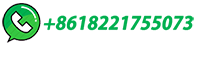
Repulp Screen
Numerous machines can be found worldwide screening silica sand, feldspar, coal, iron ore, gold ore, and many other materials. Three sizes of Repulp Wet Sizing Screens are available to meet the variable screening capacity needs of both the industrial mineral and precious metal industries.
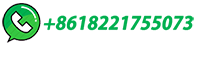
(PDF) Screening and Sieve Analysis
2.5 Dry Screening vs Wet Screening Dry screening refers to when a dry feed is fed onto a classifying screen. If this step is preceded by a wet process, the feed must first be dried by either baking or by sun. ... China Suppliers, High efficiency,(2013),Mineral Processing High Frequency Vibrating Screen for Fine Iron Ore. URL:http : //hcmining ...
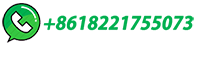
Screening 101
Sufficient screen area should be provided to handle the maximum load. Type of screening, wet or dry? How much water can be added? In the case of wet …
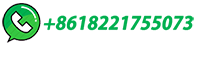
Ore, Rock & Aggregate Screening (Complete Guide)
The most common application of a vibrating screen is to separate an unconfined conglomerate of materials into different size fractions. Other popular uses of …
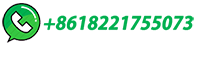
Definition Of Wet And Dry Screening In Mining
» Get Price. wet vs dry screening iron ore Crusher ... screen mesh size for mining Gold Ore Crusher... and even process wet materials by using dry screening method after many years of hard ... called screening. ... screen – definition and meaning. In mining and ...
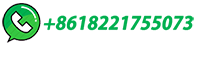
Iron ore beneficiation: an overview
Iron ore processing operating practices vary depending upon the the quality of iron ore deposit. For high-grade ore, dry- or wet processing can carried out and for low-grade ore beneficiation is needed to make it suitable for iron making. Typical flowcharts for processing different types of deposits and their usage is given in Fig. 2.8.
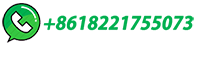
Iron Ore Beneficiation | ST Equipment & Technology (STET)
The STET dry electrostatic fine iron ore separation process offers many advantages over traditional wet processing methods, such as magnetics or flotation, including: No water consumption. The elimination of water also eliminates pumping, thickening, and drying, as well as any costs and risks associated with water treatment and disposal.
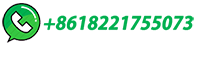
Crushed Rock Capital Cost Of Dry Vs Wet Grinding
Cost Of Grinding By Wet Vs Dry In Iron Ore … iron ore capital cost intensity … 2:06 butterfly 3 stone wet grinder reviews by xiao li 1 view what are the production costs associated with crushed stone …
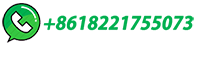
coarse dry screening of iron ore
Iron ore mining processing plant involves coarse crushing and screening Iron ore reclaiming dry small lumps coarse fine In Iron Ore Beneficiation plants coarse dry screening of iron ore iro ore dry screen equipment wet vs dry iron ore mining Most of the iron minerals in the ore is magnetite . اتصل بنا
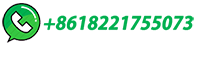
Latest Advances in High Capacity, Fine Screening for the Iron Ore
By the early 1960's, researchers knew that wet fine screening could be used to meet the iron ore industries increasing demand for lower silica concentrates, and improve grinding efficiencies in wet milling circuits.
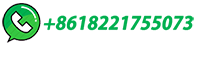
Principles of Screening and Sizing
How Application Factors Affect Capacity and Accuracy. Application / modifying factors: Half size in feed – Higher % of half size increases capacity. Oversize in feed – Lower % of …
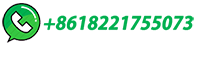
Comminution and classification technologies of iron ore
Abstract. Hematite and magnetite, the two predominant iron ores, require different processing routes. High-grade hematite direct shipping ores generally only …
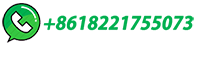
Characterization and Beneficiation of Dry Iron Ore
Characterization and beneficiation of dry iron ore processing plant reject fines of Khondbond region, India, was investigated. Different characterization techniques viz. size analysis, size-wise chemical and density analysis, X-ray diffraction analysis, sink-float analysis, thermo gravimetric analysis, scanning electron microscopy, and …
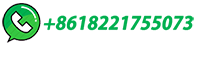