Recent development on the uses of alternative fuels in cement
The basic chemistry of the cement manufacturing process begins with calcination, the decomposition of calcium carbonate (CaCO 3) at about 900 °C to leave calcium oxide (CaO, lime) and liberate gaseous carbon dioxide (CO 2).This is followed by the clinkering process in which the calcium oxide reacts at high temperature (typically …
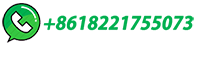
Advances in Cement Technology
The coverage of the text includes concerns regarding cement production, such as the role of volatiles in cement manufacture and in the use of cement; refractories in cement-making; and chemico-mineralogical characteristics of raw materials.
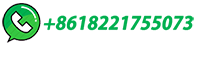
Advanced Analytics for Cement Manufacturing | IEEE …
The leading data analytics tool in the cement industry is a spreadsheet, but there is an opportunity to improve productivity and replace it with an advanced analytics application. Spreadsheets are difficult to use for process data because volume is big, sensors are many, and time-series data has noise and dropouts. Spreadsheets …
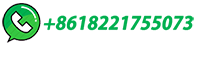
Cement Manufacturing Process- Wet and Dry Processes
Cement is a crucial building material used in construction. The Cement manufacturing process involves the extraction and preparation of raw materials, such as Limestone, clay, shale, iron ore, and Gypsum.
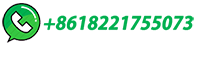
Cement Manufacturing Process
Cement Manufacturing Process. Cement is the basic ingredient of construction and the most widely used construction material. It is a very critical ingredient, because only cement has the ability of enhancing viscosity of concrete which in returns provides the better locking of sand and gravels together in a concrete mix.
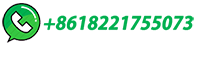
Manufacturing Cement: The Smart Way
"Advancements in gear technology have significantly enhanced the efficiency and performance of cement manufacturing processes at Wonder Cement. Modern gears, crafted from high-strength alloys and featuring advanced surface treatments, offer superior durability and wear resistance.
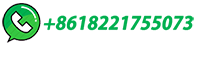
Carbon Capture in the Cement Industry: Technologies, …
For application at cement plants, partial oxy-fuel combustion, amine scrubbing, and calcium looping are the most developed (TRL 6 being the pilot system …
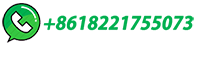
Analyzing thermodynamic improvement potential of a selected cement
Process description of the plant production line. Cement production is a complex process which includes operations such as preparation of raw materials, clinker formation and cooling to achieve a crystallographic structure that meets the required cement specifications, and finish milling.
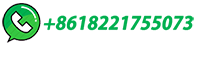
Mastering Process Control Instrumentation in Cement …
Process control instrumentation is a complex system of sensors, transmitters, controllers, and other devices designed to measure and control physical quantities such as temperature, pressure, flow, and level in an industrial process. In the realm of cement plants, process control instrumentation is the key to achieving high …
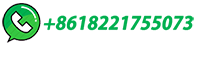
Inside the Cement Manufacturing Process
Unveiling the cement manufacturing process! Explore raw materials, energy efficiency, environmental impact, and future trends in this comprehensive guide.
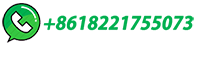
Cement and Clinker Production by Indirect Mechanosynthesis Process
Global cement production has reached 3.9 billion tons. However, the clinkerization process, which is the basis of cement production, is responsible for an approximate annual global CO2 emission of 2 billion tons. As part of CEMBUREAU's 5C strategy, the European cement industry aims to achieve carbon neutrality throughout the cement …
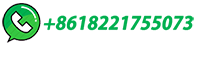
Advances In Concrete Technology | Agg-Net
Grinding aids that optimize the cement manufacturing process and reduce energy consumption are now commonplace alongside chemicals that enhance the strength performance of cement. Shrinkage-compensating admixtures This range of admixtures reduces the inherent shrinkage of concrete, which is an inevitable result of the hydration …
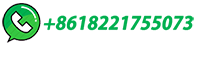
A practical guide to improving cement manufacturing …
Cement is a fine, soft, powdery-type substance made from a combination of calcium, silicon, aluminum, iron and other materials, including limestone, shells, gypsum, clay, …
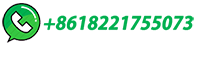
Advanced Process Control for Cement Production
The grinding stage in a cement plant is extremely energy-intensive, consuming almost half the plant's total electric power requirement. Expert systems designed for cement production, can use real-time plant data to make precise statements about the plant's quality parameters.
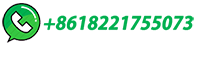
Modelling the cement process and cement clinker quality
The process model developed for application to cement manufacturing processes adequately predicted a full-scale reference case, including the amount and …
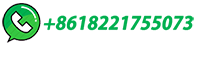
Precast concrete manufacturing: How it is made
How is precast concrete made An overview of the process of making precast concrete. The production of precast concrete structures involves several key steps, from design and mold preparation to transportation and installation. Here's a …
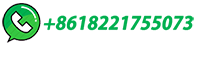
Advances in Cement Research
Advances in Cement Research highlights the scientific ideas and innovations within the cutting-edge cement manufacture industry. It is a global journal with a scope …
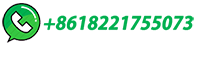
Process technology for efficient and sustainable cement production
The drivers for progress are certainly cost-based, but at the same time the cement industry, together with its equipment suppliers, has always strived to improve the overall efficiency and sustainability of the cement production process.
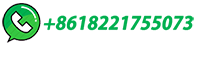
cement production | Udemy
This course provides a comprehensive overview of the cement production process, from raw material selection to the final product. You'll learn about the different types of cement, the different stages of production, and the various production processes, including kiln technology, grinding and milling, and material handling.
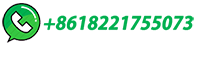
A practical guide to improving cement manufacturing …
The cement production process 1. The Quarry: The cement production process begins with the extraction of limestone and clay from the quarry. 2. Crusher and Pre-Blending: The material is then crushed to reduce particle sizes and blended to reduce variability in composition. 3. Raw Mill and Kiln: Raw materials and additives are
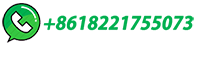
Cement Production
Cement production is an energy intensive industrial process that requires heat to be supplied at high temperature levels under the constraints of gas-solid heat exchange phenomena and the kinetics of chemical reactions.
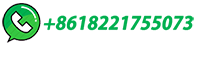
How Cement is Made
While each cement plant may differ in layout, equipment, and appearance, the general process of manufacturing portland cement is the same: crushed limestone and sand are mixed with ground clay, shale, iron ore, fly ash and alternative raw materials.
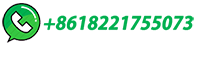
Digital Transformation of Concrete Technology—A Review
In the concrete industry, the digital transformation of concrete properties and production helps to create a more consistent and faster construction process. Availability of real-time data enables engineers to follow and control the entire production process more efficiently and with higher reliability.
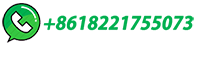
Cement | Definition, Composition, Manufacture, History,
Discover the history, composition, manufacture and facts of cement, the versatile building material used in civil engineering and construction.
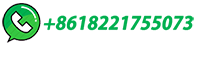
Concrete Production, Placement, & Curing Process
In this article, we explain a Short Summary of Concrete production and placement which include various stages like batching of concrete, mixing of concrete, transportation of concrete, placing of concrete, compaction of concrete, and curing of concrete. so read the article till the end.
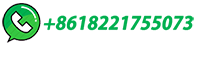
Toward smart and sustainable cement manufacturing process…
In recent years, efforts have been made to improve the sustainability of cement manufacturing through the use of renewable energy, the capture of CO 2 emissions, and partial replacement of cement with supplementary cementitious materials. To further enhance sustainability, optimizing the cement manufacturing process is …
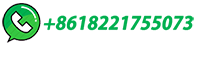
Home | Big Boss Cement Inc.
BIGBOSS Cement (BBCI) is a Filipino-owned start-up company specializing in production of environment-friendly cement in the country. Our company utilizes advanced technological infrastructure and methods that are capable of producing high-quality and environment-friendly cement.
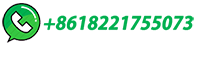
Cement-based additive manufacturing: experimental investigation of
The interest in additive manufacturing (AM) of cement-based materials is steadily increasing. Moreover, there is a growing need for higher productivity and part quality. In this study, the impact of the different values of the process parameters on part quality was identified. An alternative process-control strategy was investigated, …
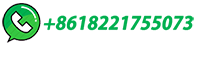
Cement Manufacturing Process | Engineering Intro
The remaining cement is shipped in bulk quantities by mean of trucks, rails or ships. Cement Manufacturing Process Flow Chart. After explaining the complete process of cement making, flow …
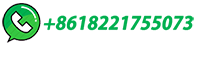
Digitization and the future of the cement plant | McKinsey
Can a fully integrated manufacturing process that has raw material–based production generate higher margins? The COVID-19 crisis has forced cement …
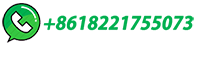