Primary Crusher Selection & Design
How you select your primary crusher will be based on factors like moisture content, maximum rock lump size, material density SG, abrasion index, degradability and it being prone to dusting or not. The crusher capacities given by manufacturers are typically in tons of 2,000 lbs. and are based on crushing limestone weighing loose about 2,700 lbs. per yard3 and …
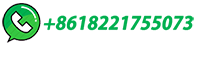
Stationary quarry rock crusher for primary crushing
A stationary quarry rock crusher for primary crushing is a machine used to break large rocks into smaller rocks, gravel, or rock dust for the purpose of primary crushing. It is typically located ...
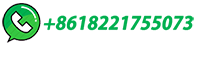
What Is Quarry Crusher
350TPH Stationary Quarry Rock Crusher Plant To Produce Aggregates in Honduras. ... Function: A secondary quarry crushing machine takes the material processed in a quarry primary crusher and further reduces it to a finer grade. The cone quarry stone crushing machine produces finer grades suitable for concrete and asphalt production.
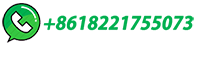
Primary Crusher Optimisation for Improved Comminution
As the term 'primary' implies, these crushers are used in the first stage on any size reduction cycle. The primary crusher is the link between chemical comminution (blasting) and the …
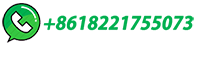
Selecting the Right Crusher for Quarry Operations | Agg-Net
First published in the September 2014 issue of Quarry Management as From Flintstone to Finesse. Sean Donaghy, national sales manager of IROCK Crushers discusses what needs to be considered when choosing a crusher. Crushing rock is an age-old idea, but the reality of the task is a far cry from that of Fred Flintstone and his good buddy Barney ...
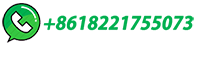
What is Quarrying?
The most common raw materials extracted at a quarry are construction aggregates such as crushed rock, sand or gravel. These abundant, yet essential raw materials, are the foundation of our homes, schools, hospitals, roads and almost all aspects of the built environment that we depend on. ... A Jaw Crusher is typically used as a "primary crusher ...
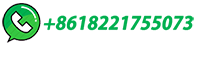
Crushing and Screening Handbook
The main target group is quarry managers, but we hope the book will be a valuable source of information for ... the crusher and scalp out fi nes. Primary gyratory crushers – ideally suited to all high-capacity primary hard rock crushing applications. Jaw crushers – we have more installed jaw crushers than anyone in the world. The lead-
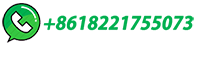
What is a Primary Crusher? | Machinery Partner
Financing Maintenance Repair Support. Company. Team Press Careers Common Questions (FAQ) Contact Us. Our Locations. 131 Dartmouth St., 3rd Floor, Boston, MA 02116 (Headquarters) 10 Mear Rd, Holbrook, MA 02343 …
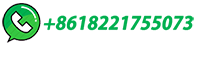
Selecting the right crusher for your operations
Best suited for secondary crushing applications, cone crushers are designed to crush pre-sized materials, usually 100mm, 150mm or 200mm, …
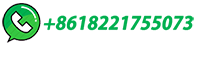
Development of a model estimating energy consumption values of primary
Most of the costs in open pit quarry operations occur in crushing and grinding processes. Therefore, the management of crushing–grinding processes is very important. Many researchers investigated the effects of pile size distribution and specific charge values occurring as a result of blasting on crusher energy consumptions and provided some cost reductions in …
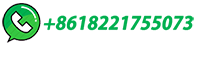
The Ultimate Guide to Crushed Stone and Gravel
The rock is typically blasted and then transported to a processing plant. Primary Crushing: The mined rock is crushed to the desired size using a primary crusher. The crusher reduces the size of the rock by breaking it into smaller pieces. Secondary Crushing: The crushed rock is then further reduced in size using a secondary crusher. This ...
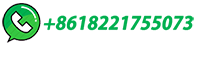
Tips for designing an efficient crushing and screening operation
Power consumption per tonne produced has more recently become a very important factor in crusher selection. Tightening the quarry shot pattern should mean less oversize material being fed to the primary crusher hopper. Not having to break or remove oversize rock in the primary hopper can dramatically improve efficiency in the system.
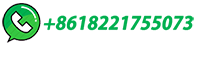
The Effects of Accelerated Blast Timing on Primary Crusher
Notable improved rock fragmentation was achieved as a result of accelerated initiation timing using electronic delay detonators. Analysis showed that primary crusher throughput of that section was 18.5 per cent higher when compared to the reference section.
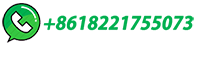
Understanding the Different Types of Crushers | Agg-Net
Jaw crushers are an excellent primary stage solution to prepare rock for subsequent processing stages, such as washing, classifying or secondary crushing. ... many jaw crushers are fed in this intermittent fashion due to gaps in the delivery of feed material from the quarry. Jaw crusher feed should be pre-screened using a grizzly prior to ...
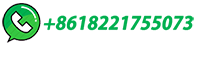
How Aggregates Are Extracted
How a rock quarry works. Rock quarries usually operate for at least 30 years and are developed in distinct benches or steps. A controlled explosion is normally used to release the rock from the working face. ... Powerful hammers or metal jaws within the primary crusher break the rock down. Rock passes through a series of screens that sift it ...
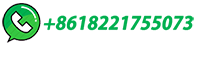
What Type of Crusher Is Best for Primary …
The right primary crusher for an application depends on several factors: Material to be crushed Feed size Desired product size Capacity required Compressive strength of the feed Moisture content The material and its …
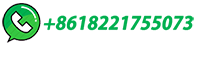
AMIT 135: Lesson 5 Crushing – Mining Mill Operator Training
Primary crusher: 3:1 to 10:1; Secondary crusher: 6:1 to 8:1; Tertiary crusher: 10:1 Therefore, if a 3 mm crusher product is required, maximum feed size to the secondary crusher would be 240 mm. Thus, the feed to the primary crusher should not exceed 2400 mm.
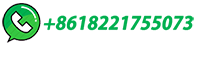
Below the surface: Setting up an underground primary jaw crusher
Below the surface: Setting up an underground primary jaw crusher. pcm_admin 04/01/2014, 2:42 pm 19/03/2020. ... Debris such as rock bolts, wire mesh, cable, pieces of pipe or wood, etc may get stuck in the scalping grizzly. ... Quarry is a must-read for quarry operators, recyclers and members of the extractive industries. The magazine informs ...
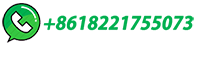
Graniterock's monumentally mobile crusher | Pit & Quarry
A primary tower sends the coarse rock to the secondary crushing circuit, and fines are moved to a wet plant. The Wilson Quarry dramatically reduces water consumption because of a plate press plant that separates water from the fines. Also, the quarry has a two-week to one-month inventory goal for most products. Moving the crusher
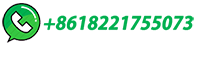
Hammer Mills
The Hammer Mill is used either as a one-step primary crusher for reducing run-of-quarry material to as small as <1-in. size, or as a secondary crusher taking 4~8-in. primary-crusher product down to <¾-in. or finer. Its use as a rock crusher is almost wholly confined to the softer, easily crushable materials such as phosphates, gypsum, barite, asbestos rock, cement rock, …
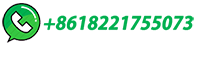
Optimization of rock primary crusher yield with the use of …
PDF | In quarries or open pit mines, the production of stones of different fractions (0.3, 3.8, 8.15, 15.25 ... etc.)requires a technological chain in... | Find, read and cite all the research you ...
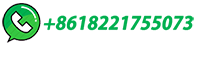
Selecting the right type of crushing equipment
A pit-portable primary crusher can be an economically sound solution in cases where the producer is crushing at the quarry face. In modern plants, it is cost-effective to use a mobile primary crusher, so it can follow the …
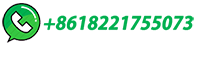
Crushing Products Size and Shape -What to Expect
The average quarry does not produce as much of this undersize rock as the average mine, but the usual practice in mining operations is to scalp off most of the undersize ahead of the primary crusher, whereas this practice is the exception rather than the rule in quarry operations.
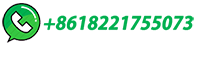
The Complete Guide to Primary Crushing, …
Primary, secondary, and tertiary crushing are three stages in the comminution process that break down large rocks into smaller pieces of varying sizes. Each stage uses different types of crushers and has distinct …
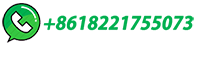
Jaw Crusher
Jaw crusher is a compression style rock crusher, useful in crushing the medium-hard to very hard material into a smaller particle size at primary crushing stage in the crushing circuit. Applications mining, quarry, construction waste …
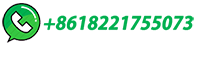
Crushers
A large primary crusher is, naturally, more expensive than a smaller one. Therefore, the investment cost calculations for primary crushers are compared together against the total costs of primary stages, including quarry face clearing, blasting, and drilling costs. In many cases, dump trucks transport the rock to a stationary primary crusher.
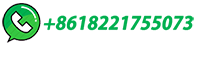
Primary Crushing
Type and size of quarry equipment. Methods employed in drilling and blasting. Method of feeding the crusher. ... Which Crusher is the Best Primary Rock Breaker. Since the minimum dimension of the feed opening of a …
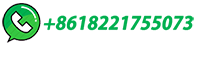
Primary Crusher vs. Secondary Crusher: …
The primary crusher's function is to reduce the size of the rock or stone for easier handling and transportation. ... While primary crushers are responsible for breaking down larger rocks and stones into smaller particles, …
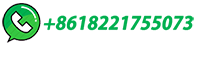
Crushing Plant Design and Layout Considerations
• Electronic control of crusher discharge opening and feed rate. With adjustment of a crusher's discharge opening, as the production continues through an on-line coarse size analysis of the crushed product (digital image analyses). Dance, A. 2001) • More attention is being paid to the impact on crushing circuit design caused by variations
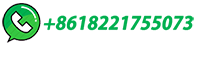
Rock Crushers & Pulverizers | Williams Crusher
Willpactor® Primary Rock Crusher. The Willpactor is an ideal primary rock crusher. Exhibiting a powerful design and rugged durability, the Willpactor® is perfect for primary rock crushing applications. Willpactors thrive in high-capacity applications such …
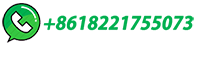