Rotary Kiln
Just as a heart must never stop beating, so a rotary kiln must never stop turning. Which is why our kilns – whether the two-pier Pyrorapid® or a classic three-pier kiln – are engineered to keep rotating, even in the most challenging of process conditions. So, you can relax with the guarantee of reliable, trouble-free operation, 24 hours a day, seven days a week.
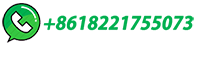
Turbu-Jet AF Rotary Kiln Burners
FCT Combustion flagship solid fuel kiln burners backed up by CFD modeling development for cement lime, iron-ore industries. Skip to content. Search for: HOME; PRODUCTS. Gyro-Therm Burners; ... Rotary kiln for all industries (cement, lime, iron-ore, kaolin, etc.) Product Details:
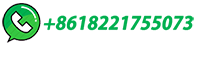
Rotary Kiln | Tanabe Co., Ltd.
ROTARY KILN. rotary kiln. A rotary kiln is a heating furnace that rotates a cylinder (retort), supplies raw materials into the furnace (inside the retort) using a feeding device (screw feeder, etc.), and uniformly heat-treats the raw materials while stirring. ... The gas burner type uses heat derived from the processed material as fuel (heat ...
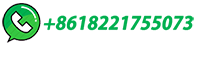
Using rotary kilns for high-temperature bulk solids processing
Rotary kilns are increasingly valued for high-temperature bulk solids processing. This article covers how they are used, how they work and what makes them so adaptable. ... Burner. In direct-fired systems, the burner is the source of combustion. Operating off a fuel source, along with combustion and dilution air, the burner provides the ...
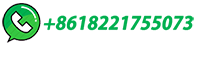
Uniflow Burner – for efficient thermal processing
FeNi Burner. Our FeNi Burner is a variant of the Uniflow Burner, as it has a third channel in which secondary air is processed. This makes it a less compact machine, but despite this downside, it is able to produce more complete combustion of fuels. These two burners aim to amplify your rotary kiln experience.
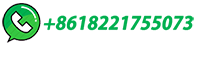
Chapter 10: Rotary Kiln
The heat transfer inside the rotary kiln produces the physical transformations and chemical reactions of the raw mix. Depending on the temperature range, there are different thermal zones inside ...
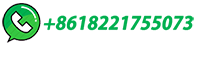
kiln efficiencies
Given the significant impact a rotary kiln burner has on the costs and revenues of iron ore pelletizing, that burner had better do its job well. The capital cost of combustion equipment is negligible in comparison to the capital cost of the plant. Yet, combustion performance is a major determinant of the pellet quality and
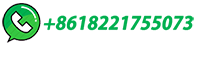
The FEECO Rotary Kiln Handbook
BURNER The burner of a rotary kiln supplies the energy required by the process. Instead of utilizing a combustion chamber, the burner on a kiln is typically mounted on the discharge/inlet end housing. Burners can be designed to accommodate a variety
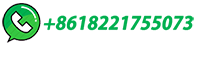
CFD modeling of rotary cement kilns
The computational models were also able to capture the intricacies of the burning zones of rotary cement kilns for changing burner-operational parameters like axial to swirl ratio and oxygen enrichment. The developed approach, computational models and simulation results will not only help in developing better understanding of cement kilns but ...
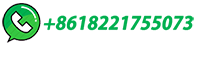
Formation and Techniques for Control of Sulfur Dioxide …
4 Due to the interaction of raw materials and kiln gases, rotary kiln systems have inherent SO2 removal efficiencies ranging between 40-99% of the sulfur input to the system. The literature suggests that 50-70% of the remaining SO2 will be removed from exhaust gases when passed through an in-line raw mill system.
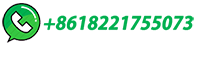
Pyro burner and combustion solutions Outotec KFS
provides a safe and effective method to heat a rotary kiln from cold start through to main fuel firing. A key to a safe kiln warm-up is the ability to provide a stable flame for an effective and controlled heat release profile. The HeatSafe Burner (HSB) design is based on our proven OptiMix™ integrated kiln burner design,
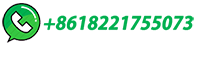
REDUCED ORDER MODEL OF A LIME KILN FOR FUEL …
The lime kiln and causticizing plant form a closed loop. There are 475 rotary kilns in kraft pulp mills globally. In the past fifty years the thermal efficiency of the lime kilns has improved from 23 GJ/tonne to around 7 GJ/tonne. In Canada, the lime kilns process from 115 tonnes CaO/day to 430 tonnes CaO/day. The burners have a thermal rating from
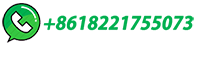
Dynasafe
Rotary Kilns are designed to destroy non-encapsulated munitions such as TNT, propellants, previously processed munitions, and small arms ammunition up to 20mm. The material is placed in a long cylindrical vessel which rotates while being heated at high temperatures for a …
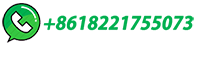
IBU-tec | The Rotary Kiln Experts for Trials and Production
In a direct-fired rotary kiln, the burner is situated inside the kiln body, that is, inside the reaction chamber. The material is heated directly by the burner flame and the stream of hot gas produced by the burner. These kilns are usually lined with refractory (heat-resistant) material so that they can be operated at higher temperatures than ...
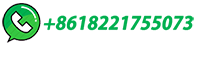
Rotary Kilns Manufacturer in India | Get Latest Price
Contact Knackwell Engineers for rotary kilns installation & application for which is installed or desired. Industrial Burners, Oven & Furnace Manufacturers in India; Enquiry Now +91-982-403-7124 +91-962-404-2423; darshan@knackwell ravi@knackwell; Home; About Us; Products. Industrial Furnace. Heat Treatment Furnace; Electric Fired ...
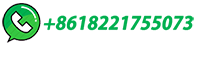
Facing Rotary Kiln Challenges? 4 Solutions to Help You!
Solution II: Easily prevent kiln ring formation Ensuring normal rotary kiln flame is one challenge; another is material looping. This occurs when furnace charge adheres in a ring shape to the inner wall of the high-temperature zone. Minor adhesion is termed kiln skin, while thicker adhesion affecting furnace operation is called ring formation.
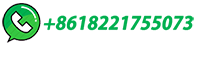
Indirectly heated rotary kiln – for efficient thermal processing
Our Indirect Rotary Kiln has been designed with a two to three-component insulated refractory lining in the heater box assembly, which helps keep heat loss to a minimum. Reduced number of fuel burners. Our Indirect Rotary Kiln has fewer fuel burners, which reduces the size of the kiln, allowing it to fit more effectively into smaller facilities.
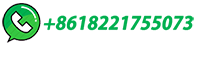
Rotary kilns for calcining and roasting | FL
We provide sturdy, tested and safe rotary kilns to keep uptime high and downtime to a minimum. Built with you in mind, the rotary kilns we offer come with a number of components that aid in safe operation and help produce superior results. Our Rotary Kilns offer significant benefits. These include the following:
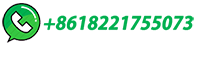
Pyro processing services Rotary kiln burner upgrades
The combustion system is designed with the flexibility to suit the following specific kiln firing applications: Wide selection of components including burner, primary air flow …
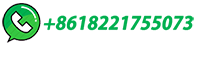
Burners for Rotary Equipment
Industrial Kiln & Dryer® services most all burners from regular maintenance, full upgrades, replacement parts and troubleshooting. FACT: Burners systems that are well maintained and serviced improves combustion efficiency which results in maximum cost savings. We have the tools, personnel and knowledge to greatly improve your current process.
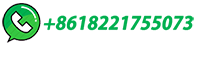
Fives | Pillard ROTAFLAM® multi-fuel burner
Our rotary kiln burner for non-cement applications . Fives' Pillard ROTAFLAM ® industrial burner has been successfully used in numerous rotary kiln applications worldwide for more …
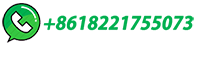
CFD MODELING OF A CEMENT KILN WITH MULTI …
temperature, and gas components in a cement rotary kiln were obtained by numerical simulation of a 3000 t/d rotary kiln with a four-channel burner. A zone wise heat flux model was presented which accounted for the thermal enthalpy of the clinker formation process and gave more insight to fluid flow, temperature, etc. within the cement rotary kiln.
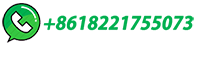
Rotary Kiln Maintenance – Get the most out of your …
Get to know your kiln Rotary kilns have many moving parts and as the kiln ages, these parts can start to move very differently. Whether you're a kiln expert or a newcomer, it's always important to review the basics, starting with the key components that make up your kiln. To help you best maximize efficiency, availability, and longevity of your
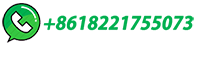
Unitherm Cemcon
The patented M.A.S. rotary kiln burner offers essential advantages compared to conventional burner systems. The complete primary air flow is brought into an adjustable swirl with a minimum of losses. Read more. The M.A.S. kiln …
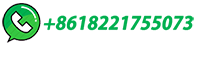
Everything you need to know about Kiln Burning Systems
A typical multi-fuel burner used in a rotary kiln is shown in Figure 3.1.12. Figure 3.1.12. Typical multi-fuel burner. Excess Air Levels. One symptom of combustion problems is the need to …
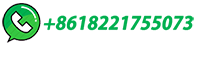
Rotary Kiln Burners | NorthStar Combustion, Inc. | Low …
Rotary Kiln Burners from Northstar are operator friendly, efficient, versatile, low NOx, multi-fuel capable, industrial hardened, and much more. Look to us. Preferred Supplier. to the Rotary Kiln Industries. 3443 West Mill Road, Milwaukee, WI 53209 USA; 1 (414) 352-2700 | 1 (414) 352-2702 .
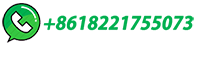
Types of Rotary Kilns
This member in the group of rotary kilns is also widely known under the term Grate Process Kiln or Lepol Kiln. These kilns are as efficient in matters of fuel consumption as the most modem preheater and precalciner kilns. Output rates, however, lag behind the aforementioned types of kilns. However, it is advantageous to select a Grate Process ...
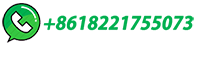
Rotary Kiln Incinerators on the Rise in Waste Management
The rotary kiln is followed by a secondary combustion chamber with a separate burner that burns off any residual hazardous components remaining in the flue gas stream after the rotary kiln. Waste with a high heating value can be used as a fuel source for the kiln itself, or for the secondary combustion chamber to further improve the ...
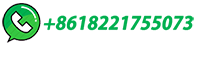
EVERYTHING YOU NEED TO KNOW ABOUT FUEL SYSTEMS IN ROTARY KILN
Previous Post Contents1 EVERYTHING YOU NEED TO KNOW ABOUT FUEL SYSTEMS IN ROTARY KILN1.1 FUEL HANDLING AND COAL GRINDING1.2 FUEL BURNERS AND FLAMES1.3 TESTING COAL BURNERS FOR TIP VELOCITY EVERYTHING YOU NEED TO KNOW ABOUT FUEL SYSTEMS IN ROTARY KILN FUEL HANDLING AND COAL …
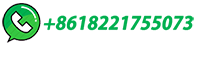
On the use of alternative fuels in rotary kiln burners — An
A homogenous heating of the pellet bed along the length of the kiln is desirable to obtain the optimum temperature–time history for the sintering of the iron ore pellets. In the rotary kiln process, the fuel is supplied in a burner at the back-end of the kiln and the aim is hence to create a long flame extending far into the rotary kiln.
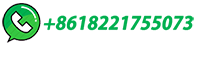