Is ore-sand the solution to the mining industry's waste …
Ore-sand and circular mining – the way forward. When it comes to the circular economy, many in the mining industry frequently relate this concept to the repurposing of waste materials generated within the traditional 'take-make-usedispose' model that prevails in the sector.
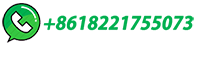
Iron Ore in India, Types, Uses, Distribution, World Map
India Ranks 4th in terms of iron ore production. Know more about Iron Ore, its Types, Distribution in India & world, Map in this article for the UPSC exam.
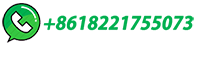
8.2: Mining and Ore Processing
When ore is first processed (typically close to the mine) it is crushed to gravel-sized chunks and then ground to a fine powder and the ore minerals are physically separated from the rest of the rock to make a concentrate. At a molybdenum mine, for example, this concentrate may be almost pure molybdenite (MoS 2). The rest of the rock …
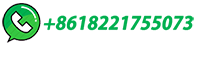
Iron processing
China, Brazil, Australia, Russia, and Ukraine are the five biggest producers of iron ore, but significant amounts are also mined in India, the United States, Canada, and …
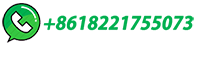
Mining | Definition, History, Examples, Types, …
mining, process of extracting useful minerals from the surface of the Earth, including the seas.A mineral, with a few exceptions, is an inorganic substance occurring in nature that has a definite chemical …
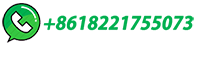
A review of ironmaking by direct reduction processes: …
Strezov mixed iron ore with biomass wood waste in different ratios and found that, the iron ore was successfully reduced to metallic iron phase when up to 30% by weight of biomass was introduced (Strezov, 2006).
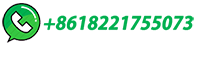
Iron ore | BHP
How is iron ore mined? From pit to port, our iron ore undergoes a series of processes before export. First, we explore the geology of the region to find the best iron ore prospects for our operations. Once the ideal site has been chosen, the ore is drilled and blasted. It is then transported to the primary crusher for processing.
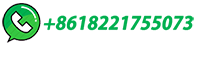
Environmental Impact of Steel
The main ingredient in the production of steel is iron ore mined from Earth. Over 2,000 million tons of iron ore is mined mined a year - about 95 percent is used by the steel industry. Iron ore is the world's third most produced commodity by volume - after crude oil and coal - and the second most traded commodity - only beaten by crude oil.
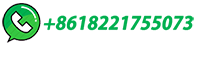
Ironmaking 101 – From Ore to Iron with Blast Furnaces
The first step in the production of steel or cast iron alloys is the reduction of iron ore, which contains iron oxide and gangue or mineral impurities, to unrefined hot metal or pig iron. The blast furnace is currently the key tool for ironmaking.
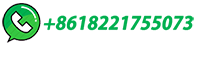
Iron Ore | Geoscience Australia
The company has no immediate development plans for the Wiluna West iron ore deposit but reported in August 2019 that it had executed a "Term Sheet for a Mining Rights Agreement" with Gold Valley Iron Ore Pty Ltd to mine up to 3 Mt of iron ore from the project's John William Doutch deposit 54.
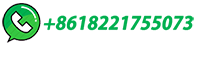
Why Is Iron Ore Valuable? Behind the Scenes of Production …
Learn about the extraction and production process of crude iron ore, along with which countries mine and store the most. See what experts say.
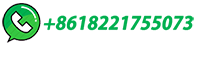
Energy and Environmental Profile of the U.S. Mining …
4.1.1 Iron Ore Mining There are two basic methods of mining iron ore. These are: • Surface mining or open-pit mining • Underground or shaft mining To be competitive, iron mining must be done on a very large scale. Surface mining is the preferred choice, although there are exceptions. Small, low-capacity mines have rapidly disappeared.
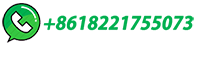
Mining iron ore
Iron ore is an ore always in demand, due to its use in producing iron and steel bars via Smithing. There are many locations to mine iron ore, but the Mining Guild features several advantages; a set of iron ore rocks that are extremely close to a deposit box, an invisible +7 boost to mining, a 50% reduced ore respawn timer (which means you never …
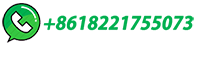
How Gold Is Mined | Gold Mining Process | World Gold …
The actual mining of gold is just one step of the gold mining process. Learn how gold is mined and the five stages of a large scale gold mining project.
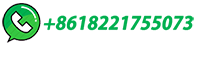
The six main steps of iron ore processing
When iron ore is extracted from a mine, it must undergo several processing stages. Six steps to process iron ore. 1. Screening. We recommend that you begin by screening …
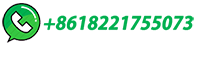
Exploring Steel Production: A Comprehensive Visual Process …
The Journey from Iron Ore to Steel: An Overview. The transformation of iron ore into steel is a remarkable process that involves a series of detailed steps. Beginning with the extraction of iron ore from the earth through mining operations, this raw material is then treated and prepared for the smelting phase. The extracted ore …
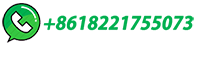
The stages of mining: 5 lifecycle processes explained
This is a definitive breakdown of the stages of mining. Learn exactly how ore is mined from this expert-approved guide.
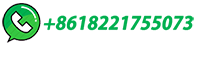
Introduction: Overview of the global iron ore industry
This chapter first provides an overview of world iron ore production and trade, as well as reserves and resources, followed by a summary of the key mining operations …
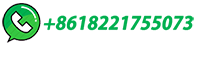
[VIDEO] The History and Process of Silver Mining
The process of mining for silver. The process of mining for silver is broken down into three steps: removing ore from the earth, breaking it down and then flushing the silver from ore.
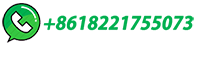
Investigation into the characteristics of H2-rich gas injection …
Semantic Scholar extracted view of "Investigation into the characteristics of H2-rich gas injection over iron ore sintering process: Experiment and modelling" by Xiao-xian Huang et al.
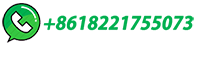
Australia's Iron Ore Industry: Challenges and Outlook 2024
Delve into the complexities of Australia's Iron Ore Industry in 2024, impacted by China's economic slowdown and shifting global demand.
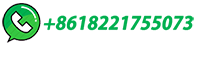
Iron Ore Processing, General
Making iron and steel from iron ore requires a long process of mining, crushing, separating, concentrating, mixing, agglomeration (sintering and …
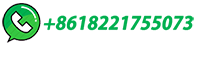
Low grade Iron Ore Beneficiation and the Process of Jigging
Due to this reason the availability of high grade iron ore is reducing and the supply of high grade iron ore to iron and steel plants is declining sharply. Hence, the scenario is steadily shifting towards the use of low grade iron ores and slimes which are stock piled in the mine's sites for years.
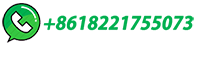
Understanding Iron Ores and Mining of Iron Ore – IspatGuru
The process of mining of iron ore from discovery of an iron ore deposit body through extraction of iron ores and finally to returning the land to its natural state consists of several distinct steps. The first is discovery of the iron ore deposit, which is carried out through prospecting or exploration to find and then define the extent ...
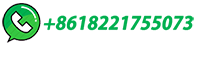
Iron processing | Definition, History, Steps, Uses, & Facts
Iron ore processing is a complex and vital process that transforms raw iron ore into usable steel. From exploration and extraction to grinding, beneficiation, and …
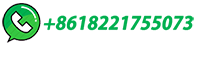
Mining Sector in India
The Mining sector in India is one of the core industries of the economy. It provides basic raw materials to many important industries. India is a major producer of numerous metals and minerals.
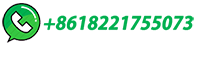
Ironmaking 101 – From Ore to Iron with Smelting and Direct Iron …
While the blast furnace remains an important tool for ironmaking, newer technologies such as smelting and direct iron reduction are available to produce iron with minimal byproduct generation and slag-free hot metal. Smelting reduction and direct iron reduction can reduce energy input, lower greenhouse gas emissions and minimize slag …
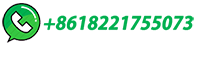
Iron ore beneficiation: an overview
This chapter briefly discusses the current scenario of iron ore resources in India and future challenges emerging due to the depletion of high-grade ore reserves and a change in the ore cut-off grade to 45% Fe. Mining methodology for open-cast iron ore mine is also covered.
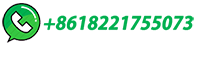
Sintering: A Step Between Mining Iron Ore and Steelmaking
Learn about the technology used in sintering, the process that converts fine-sized raw materials, including iron ore, limestone, etc. into product for blast furnace.
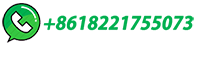
The Direct Reduction of Iron
Only rarely now can run-of-mine ore be used directly in an ironmaking process, due to high impurity levels. Generally the most economical way to remove impurities is to crush and grind the ore until impurity minerals are liberated, and then separate these minerals from the desired iron-containing phases.
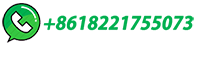