MINI-PELLETIZING: CRISIS AS AN OPPORTUNITY FOR INNOVATION …
also added to the design for the new Circular Mini Pellet Plant - CMPP (Figure 2). The feed preparation for the CMPP, ... further segregation into hearth layer and finished product.
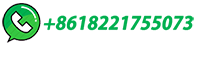
Iron Ore Pelletizing Process: An Overview | IntechOpen
A layer of indurated pellets is arranged at the bottom of each car to protect it against the heat. The green pellets are then charged on top of the hearth of indurated pellets. ... Mourão J, Huerta M, de Medeiros U, Cameron I, O'Leary K, Howey C. Guidelines for selecting pellet plant technology. In: Proceedings of the 6th International ...
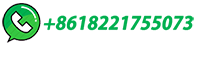
Optimization of Pellet Plant Straight Grate Induration
Indian iron ores are suffering from high amounts of alumina and loss on ignition (LOI), which are deleterious constituents in both the pelletizing as well as iron making processes. Iron ore fines utilized in pellet making consist of alumina in the range of 3.20–3.35% and LOI in the range of 3.50–3.70%. Detailed palletization studies have been carried out on high alumina …
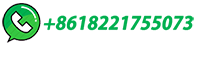
A Computational Study on the Reduction Behavior of Iron …
A phenomenological model for the reduction of iron ore/carbon composite pellets in a multi-layer bed rotary hearth furnace has been developed. A single pellet model has been scaled up to a multi-pellet layer version in a computationally efficient way. The multi-layer pellet bed has been conceived as single column of identical pellets in a rectangular enclosure, …
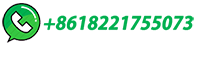
Process flow diagram of pelletization unit
The First Grate Kiln System pellet plant was installed in 1960. The plant used iron ore concentrate as input and produced superior iron ore pellets for blast furnace and direct reduced iron feed ...
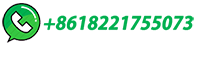
Iron Ore Agglomeration Technologies | IntechOpen
Until the 1950s of the last century, the oxidized iron ores that were loaded into the blast furnace had granulometries within 10 and 120 mm. However, the depletion of high-grade iron ore sources has made necessary the utilization of concentration processes with the purpose of enriching the iron ore. Because of these processes, a fine granulometry is produced, and …
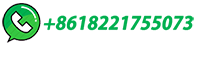
Traveling Grate Pelletizing Plant
Pellet hardening (indurating) Hearth layer and product screening ; In order to adjust the moisture content, water is added in the mixing step. The ore is then mixed with small amounts of binding agents. Fluxes such as limestone, …
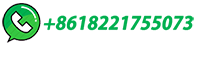
Understanding Sinter and Sinter Plant Operations – …
To avoid a direct drop of feed onto the grate, a hearth layer of about 25 mm to 50 mm of coarse (already sintered) material is fed first onto the traveling grate. Feeding devices typically include a roll feeder in conjunction with chutes which act to …
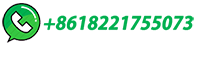
Influence of Pellet Basicity (CaO/SiO2) on Iron Ore Pellet …
The hearth layer pellets protect the grate bars from high gas temperatures. The green pellets contain 8 to 9% free moisture and are 8 to 16mm in size. The travel ling grate carries the pellets ... steel baskets (500mm long) and fired in pellet plant indura-tion machine. The stainless steel basket was kept in the cen-
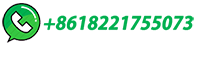
Atlas Pellet Plants Closing Down | Hearth Forums Home
Atlas Pellet Plants Closing Down. Thread starter tchdngrnby; Start date Dec 23, 2010; Active since 1995, Hearth is THE place on the internet for free information and advice about wood stoves, pellet stoves and other energy saving equipment. We strive to provide opinions, articles, discussions and history related to Hearth Products and in a ...
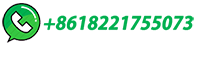
Pelletizing Process
the company built a plant at its Kobe Works in 1966. This paper introduces the history of pelletizing plants, including process outlines and the latest achievements in the construction of plants overseas. In the past, plant owners had focused mainly on the quality of the product pellets and plant equipment, as well as the cost of the plants.
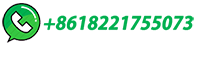
Sinter Plant Operations: Hazardous Emissions | SpringerLink
The release of dioxins was detected at two different positions. The first release position was located at the point where the drying zone reached the hearth layer, showing a broad peak containing a large amount of furans. The second release position was located at the point where the melting zone reached the heath layer, showing a sharp peak.
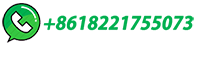
Dynamic simulation of pellet induration process in straight …
The grate bars fixed on a moving strand are first covered with a layer of burnt pellet, known as hearth-layer. The green pellets containing 7 to 9 wt.% free moisture and 10 to 14 mm in size are then fed onto this layer and travel together with the sub-layer through several thermal zones of the furnace.
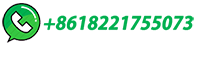
Samarco Gets Record Pellet Production From a Single Plant …
recently reported that Samarco Mineração S.A. set a monthly production record during August 2023 of 824,829 metric tons (mt) of high-grade pellets in a single pelletizing line with its 816-m 2 Pelletizing Plant Indurating Machine #4 at the company's Ubu site in Brazil. On an annual basis, the production is equivalent to approximately 8.8 to 9 million mt/y of pellets in a …
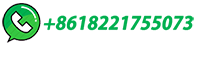
Outotec Pelletizing tech 300507
Our pelletizing process uses hearth and side wall layers, consisting of indurated pellets recirculated from production and enabling the fi ring of the entire bed of green pellets and …
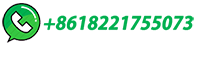
2.0MTPY Iron Ore Pelletization Plant
CAPACITY ENHANCEMENT OF PELLET PLANT FROM 2.0 TO 2.5 MTPA MONNET ISPAT AND ENERGY LIMITED Raigarh, CG Prepared By Fe Techno Engineering and Power Solutions Bangalore -560 004 ... Using bigger size pellets as hearth layer will help to overcome the pallet grate bar choking . MONNET ISPATAND ENERGY LTD., RAIGARH
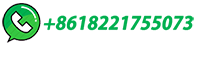
PRE-FEASIBILITY REPORT of Proposal for 2.4 MTPA Pellet Plant
The hearth & side layers bin shall be load cell mounted. g) Hearth Layer Separation / Product Screening Building (HLSB) HLSB has two functions. Two separate pellets are required as hearth and side layer on the Indurating machine and also to screen out undersize fines pellets.
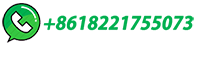
Schematic of the straight grate pelletizing process.
SG process consists of a single furnace which encloses an endless chain of pallet cars ( Figure 5).At the feed end of the furnace, a small layer of indurated pellets known as the hearth layer is ...
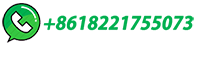
Sintering Technology for Iron ores and Optimization of
The sinter strand consists of several pellet cars and can be regarded as an unlinked endless chain because of its motion. Due to it, the pallet cars are subject to stresses resulting from the following. ... Further, these two parameters are ideally to be individually controlled which is normally difficult in a sinter plant. Hearth layer .
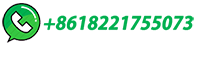
Pellet Plant Products || KOBE STEEL, LTD.
Pellet Plant; Home > Products > Iron Unit Field > Pellet Plant. ... because of exellent heat recuperation and lower pressure drop of process gases by eliminating hearth layer. RICH KNOW-HOW. KOBE STEEL is operating a pelletizing plant in its integrated steel complex in order to feed the various pellets to Blast furnaces. Through experience of ...
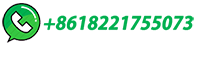
Compact-sized Pellet Plant
3. Pellet hardening (indurating) 4. Hearth layer and product screening In the mixing step, the iron ore concentrate is mixed with additives and water is added to adjust the raw mix moisture …
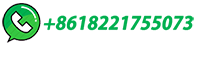
A Mathematical Model for Straight-Grate Iron Oxide …
covered by a thin layer of previously fired pellet known as hearth layer. The green pellets are fed above the hearth layer to form the green pellet bed, which enters into the furnace from …
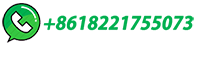
Mathematical model for a straight grate iron ore pellet …
A hearth layer of fired pellets is used in the former to protect grate bars from excessive heating. Fresh pellets are charged onto a hearth layer of the fired ones. ... For any particular plant and pellet characteristics, there are a set of optimal furnace operational conditions and pellet carbon content. For KSC plants considered here, the ...
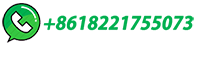
Ash leak, help! | Hearth Forums Home
I have a Pleasant Hearth PH50CABPS Series Cabinet Pellet Stove. Lately I've noticed a fine layer of white ash/dust coating some things in my house. This isn't good at all, my father has breathing problems and I need to resolve this. ... but I believe you need to go back to a central heat plant with a humidification unit and electrostatic ...
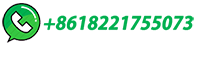
Mathematical model for a straight grate iron ore pellet …
A hearth layer of fired pellets is used in the former to protect grate bars from excessive heating. Fresh pellets are charged onto a hearth layer of the fired ones. ... For any particular plant and pellet characteristics, there are a set of optimal furnace operational conditions and pellet carbon content. For KSC plants considered
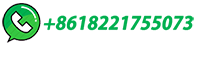
Fire at Maine Wood Pellets plant | Hearth Forums Home
Active since 1995, Hearth is THE place on the internet for free information and advice about wood stoves, pellet stoves and other energy saving equipment. ... Pellet plants tend to burn. Making them fire-resistant costs money and they are low margin operations. I think most owners balance cost for occasional fires against the costs required ...
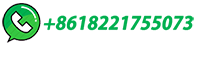
Reduction of Iron-Oxide-Carbon Composites: Part II. Rates of …
A new ironmaking concept is being proposed that involves the combination of a rotary hearth furnace (RHF) with an iron-bath smelter. The RHF makes use of iron-oxide-carbon composite pellets as the charge material and the final product is direct-reduced iron (DRI) in the solid or molten state. This part of the research includes the development of a reactor that …
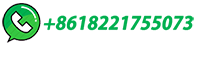
Novel Methodology of Modeling Iron Ore Induration …
The model was validated against reference plant operating data and then used to improve the operational efficiency of an induration furnace. Keywords: Induration Furnace, Computational Fluid Dynamics, Iron Ore, Straight Grate, Pelletizing, Green House Emissions ... In a straight-grate machine, a hearth layer of hardened pellets is loaded onto ...
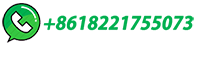
Dynamic simulation of pellet induration process in …
first covered with a layer of burnt pellet, known as hearth-layer. The green pellets containing 7 to 9 wt pct free moisture and 10 to 14 mm in size are then fed onto this layer and travel …
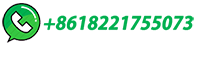