Secondary Impact Crusher | HSI
The new HAZEMAG concept combines the knowledge gained from over 70 years of crusher design and manufacture, with the practical experience and operational needs of plant operators. The HSI series of secondary impactors have been designed for economic crushing and, depending on how the equipment is configured, are capable of processing either ...
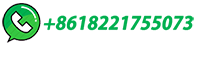
Impact Crusher
In the working process of the machine, the rotor rotates at a high speed driven by the motor. When materials enter the crushing chamber, they will be impacted and crushed by the blow bar on the rapidly turning rotor, and then thrown to the impact plate for a secondary breaking, finally rebounded back to the rotor area and be crushed again.
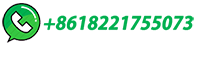
Understanding the Different Types of Crushers | Agg-Net
Jaw crushers are mainly used in primary crushing stages and are rarely used for secondary crushing. As a compression crusher, this type of machine generally produces the coarsest material because it breaks the rock along its natural lines of weakness. ... as this can cause problems downstream at the secondary processing plant. In practice, many ...
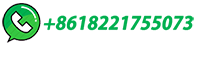
Types of Crushers: What You Need to Know | Machinery …
Gyratory Crusher Secondary crushing equipment. After materials go though their first round of crushing, they are fed into a secondary crusher to be broken down further. The average input size for a secondary crusher ranges from 13" to 4" during this stage. Secondary crushing is especially important for making graded material that is going on to ...
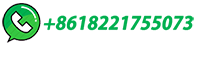
AMIT 135: Lesson 5 Crushing – Mining Mill Operator Training
Primary crusher: 3:1 to 10:1; Secondary crusher: 6:1 to 8:1; Tertiary crusher: 10:1 Therefore, if a 3 mm crusher product is required, maximum feed size to the secondary crusher would be 240 mm. Thus, the feed to the primary crusher should not exceed 2400 mm.
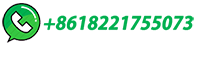
Construction Working and Maintenance of Crushers for …
Efficiency of a multiple stage crushing plant can be maximized by operating a primary crusher at a setting which produces a satisfactory feed size for the secondary crusher and operating …
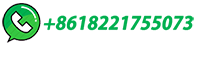
Primary Crusher
Secondary coal crusher: Used when the coal coming from the supplier is large enough to be handled by a single crusher. The primary crusher converts the feed size to one that is acceptable to the secondary crusher. ... Designing Green Cement Plants. Book • 2015. Expert Systems with Applications. Journal. Wills' Mineral Processing Technology ...
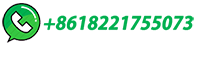
Crushers and Grinders in Cement Plants
Advantages of Crushers and Grinders in Cement Plants: Enhanced Productivity: ... Secondary Crushers: Following the primary crushing stage, secondary crushers take center stage, further reducing ...
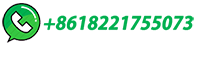
Complete Lecture about Crushers in Cement …
In the cement industry the jaw crusher is in general use; this is due to its relatively simple design and also to the circumstance that this crusher is manufactured in large units. ... Fig. 3.28. shows a two-stage crushing plant …
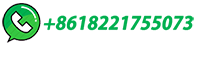
(PDF) Process Automation of Cement Plant
The secondary crusher (SC) is started together with C2. ... The objective of this article is the development of a novel raw material mix proportion control algorithm for a cement plant raw mill ...
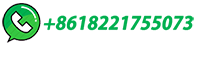
Cement Equipment In Cement Plant | AGICO …
Besides, we provide cement production line, stone crushing plant, etc. Skip to content. Blog. Contact. About. Cases. Factory. CONTACT US. info@cementplantequipment. CALL US +86 . REQUEST A …
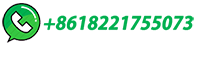
A Comprehensive Guide to Secondary Crusher Types
Learn about the different types of secondary crushers, including impact crushers, cone crushers, roll crushers, and jaw crushers, and their functions, advantages, disadvantages, applications, and factors to consider when selecting them. Discover case studies and examples of successful applications, as well as future developments in secondary …
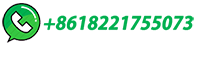
what type of crusher machine are used in cement plant
In cement plants, various types of crusher machines are used to crush raw materials into smaller particles suitable for the cement manufacturing process. The primary types of crusher machines used ...
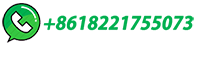
Cement Crusher | Crushers for Cement Plant
AGICO offers 4 types of crushers for cement plants: hammer crusher, jaw crusher, impact crusher, and cone crusher. Hammer Crusher. INQUIRY. CHAT NOW. The hammer crusher is a kind of crushing machine which uses impact …
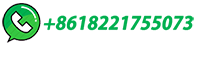
What Is Primary, Secondary, and Tertiary Crushing?
The degree to which material is reduced through stages of primary, secondary, and tertiary crushing can depend on the type of material, like aggregate, concrete, and asphalt, and can also depend on the variety of …
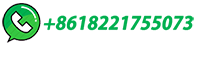
Construction Working and Maintenance of Crushers for …
Efficiency of a multiple stage crushing plant can be maximized by operating a primary crusher at a setting which produces a satisfactory feed size for the secondary crusher and operating the secondary crusher (or the last stage crusher) in a closed circuit. Glossary of Terms Breaker Block (Breaker Plate) The steel surface of a crusher against ...
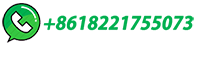
Everything you need to know about cement …
In a cement plant, crushing is the primary size-reduction process carried out under the action of external mechanical forces. Generally, three levels of crushing are recognized: coarse (top product size, up to 150 to 200 mm), …
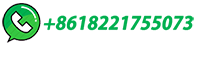
Demystifying the Crusher Plant: A Comprehensive …
Tertiary Crushing Section: Fine-Tuning the Stone Sizes:-After the secondary crushing the aggregates are sent to the sieving plant where they are separated and transported to their respective subsite using a conveyer belt, …
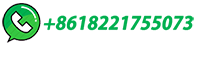
Everything you need to know about Crushers in Cement …
The roller crushers are used for moist and sticky materials. Generally the machines have to be rigid enough to crush also hard inclusions. As the reduction ratio is only about 5:1 a 2-stage crushing is required in most applications. …
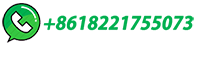
Types of Crushers: Choosing the Right One for Each Stage
Medium crushing: Employ cone crushers or impact crushers in secondary crushing to further reduce material into smaller particles. Fine crushing: Utilize sand making machines, roll crushers, fine crushers or compound crushers in tertiary crushing to produce fine sand or powder. 4. Capacity requirements Determine the hourly capacity needed.
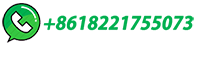
P&Q University Lesson 7: Crushing & Secondary Breaking
Lesson 7 of the Pit & Quarry University handbook discusses crushing and secondary breaking equipment. ... There are then two options for processing the bulk material after it has been reduced to feeding size of the crushing plant: mobile or stationary plants. ... For crushing demolition concrete, look for a high-performance electro- or ...
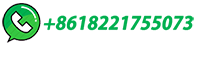
Crushing Plant Flowsheet & Design-Layout
Standard (Secondary) Cone Crusher (Refer to Fig. 1): The Standard Cone crusher is normally applied as a secondary crusher in a multi-stage crushing circuit. The small diameter feed distributor and the wide throat opening at the top of the liners enable the Standard Cone crusher to accommodate the larger feed produced by the Primary crusher.
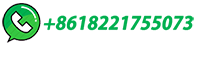
Cement Manufacturing Process
Hammer Crushers: – In DMC, these are mainly used for crushing of correctives, pumice, coal and clinker. They are used for size reduction of hard to medium grain size and sometimes for wet and sticky material. Hammer mills work with reduction ratios as high as 1:40 to 1:60 as primary and 15:1 as secondary crushers. It can be installed for ...
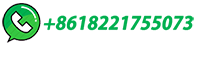
What Machines Do Stone Crushing Plants Need? | Fote …
4. Hammer crusher A hammer crusher is a special type of crusher that consists of a rotor with disks on which the hammers are mounted and articulated in the outer area. They, therefore, have a design similar to horizontal impact crushers. The rotor's high flywheel mass enables the single-stage shredding of feed pieces with edge lengths of up to 1,800 mm to less …
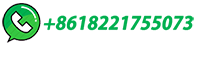
Secondary Impact Crushers – MEKA
APPLICATIONS The strength of Secondary Impact Crusher (MSI) makes them ideal for diverse applications and configurations. They have proven their effectiveness in a host of missions from crushing low abrasive materials to industrial applications and are suitable for quarrying and gravel pit industries, cement industry, concrete and asphalt recycling, and slag recycling.
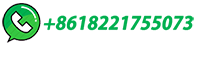
Cement Crusher – Crusher In Cement Plant | AGICO Cement
Raw materials of the cement plant are mostly from open-pit mines, and the ore usually has a large particle size. In the preparation of cement raw materials, we first need to crush limestone, gypsum, clay, and other materials into proper size to facilitate the subsequent transportation and storage, at the same time make full preparations for the next process (cement raw materials …
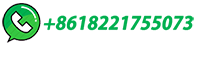
Primary and Secondary Crushing: Understanding …
The secondary crusher is the equipment that reduces the size of the materials further, after they have been reduced by the primary crusher. The secondary crusher has a size reduction ratio ranging from 3:1 to 5:1. The …
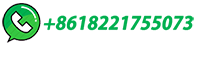
11.19.2 Crushed Stone Processing and Pulverized …
Quarried stone normally is delivered to the processing plant by truck and is dumped into a bin. A feeder is used as illustrated in Figure 11.19.2-1. The feeder or screens separate large ... the scalping screen is processed in the secondary crusher. Cone crushers are commonly used for secondary crushing (although impact crushers are sometimes ...
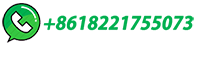
Cement Crusher | Crushers for Cement Plant | AGICO Cement …
AGICO offers 4 types of crushers for cement plants: hammer crusher, jaw crusher, impact crusher, and cone crusher. Hammer Crusher. The hammer crusher is a kind of crushing machine which uses impact energy to crush materials. It is mainly composed of shell, rotor, impact iron, lining plate, and screening strips. The shell is divided into upper ...
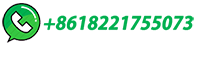
P&Q University Lesson 7: Crushing & Secondary …
In the weight class up to 77 tons (70 metric tons), they can be used for both stone and recycled concrete and asphalt aggregates processing as a classic primary crusher for natural stone with an active double-deck …
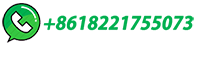