Environmental impacts and decarbonization strategies in the cement …
The use of cement and concrete, among the most widely used man-made materials, is under scrutiny. Owing to their large-scale use, production of cement and concrete results in substantial emission ...
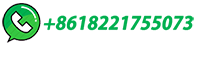
NC DAQ extends air permit for Carolinas Cement project
The amended regulations will maintain dramatic reductions in mercury, acid gases, particulate matter and total hydrocarbons from existing cement kilns across the …
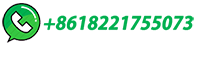
Cement Kilns Technical Support Document for the NOx …
There are four different types of cement kilns used in the industry: long wet kilns, long dry kilns, kilns with a preheater, and kilns with a precalciner. The long wet and dry kilns and
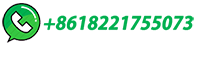
Update on electric cement kilns
Namely: heat transfer with plasma in rotary kilns; direct separation of carbon dioxide from calcination of carbonate-based raw materials in the production of cement clinker and burnt lime; and carbon dioxide-free products with electrified production - reactivity of cement clinker with secondary additives.
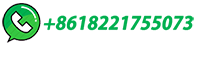
SOUTH CAROLINA CEMENT INDUSTRY
SOUTH CAROLINA CEMENT INDUSTRY. PORTLAND CEMENT MANUFACTURING AND USE. Portland Cement Association (PCA) represents 93% of US cement manufacturing capacity with over 90 plants in 32 states and distribution facilities in every state in the …
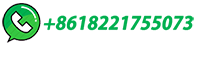
Cement Kiln
The Cement Kiln is a Crafting Table created at the Assembly Line. It is used to create Cement and Reinforced Concrete for building purposes. The Cement Kiln requires Iron Pipe to avoid buildup in the output.
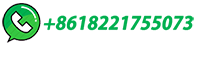
Cement Kilns: Design features of rotary kilns
Design features of rotary cement kilns. The shell of the kiln is made of mild steel plate. Mild steel is the only viable material for the purpose, but presents the problem that the maximum temperature of the feed inside the kiln is over 1400°C, while the gas temperatures reach 1900°C.
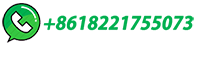
South Carolina
The largest 10 kilns in the country account for 22% of the country's total capacity and these were all built after 2000. Then, the next 44% of the national capacity …
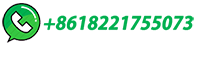
OHIO CEMENT INDUSTRY
Cement is manufactured by heating lime, silica, alumina, iron, and other materials at high temperature. The resulting substance is a marble-like ball called clinker that is ground, mixed with limestone and gypsum, and used to create concrete.
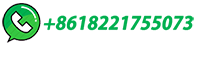
NORTH CAROLINA CEMENT INDUSTRY
The resulting substance is a marble-like ball called clinker that is ground, mixed with limestone and gypsum, and used to create concrete. The U.S. cement industry has long …
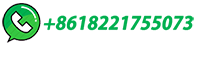
Cement in the USA
The US$750m deal saw the transfer of the Harleyville, South Carolina and Roberta, Alabama cement plants, a cement grinding station in Altanta, Georgia, cement terminals and ready-mix units. ... It added a third cement kiln at Midlothian in 1967 and announced the Hunter cement plant near New Braunfels in south Texas in 1978. Hunter …
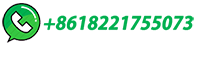
Alternative Fuels in Cement Manufacturing | IntechOpen
The wastes used as alternative fuels in cement kilns would alternatively either have been landfilled or destroyed in dedicated incinerators with additional emissions as a consequence. Their use in cement kilns replaces fossil fuels and maximises the recovery of energy.
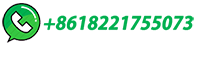
Comprehensive Guide to Cement Kilns: Processes, Types, …
Cement kilns are an essential component of the cement manufacturing process, playing a crucial role in producing the clinker that is ground into cement. These massive, rotating cylindrical vessels are designed to withstand extreme temperatures and chemical reactions that transform raw materials into clinker.
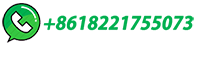
Giant Cement Company | News
We are proud to announce that our Giant Cement Plant in Harleyville, SC, was awarded with the 2022 Environmental Performance Award in recognition of our improvements that will replace approximately 25,000 metric tons of coal with natural gas in our kiln system, reducing carbon dioxide emissions by an estimated of 26,000 metric tons.
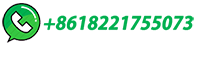
Cement Plants located in United States
Cement plant locations and information on United States can be found below. For full access to the database, purchase The Global Cement Report™, 15th Edition.
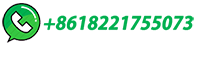
GCHI
The Harleyville plant went through major expansions in 1952, 1957, 1962, and 1974, including the installation of multiple kilns and the first baghouse used on a wet kiln. The commissioning of new dry-process kilns to replace the wet-process kilns took place in 2005. The new parent company Giant Cement Holding, Incorporated (GCHI), was …
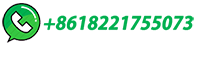
GCHI
The soft limestone/marl of South Carolina was much easier to mine than the hard limestone of the Pennsylvania Lehigh Valley, leading to increased production at the new site. The …
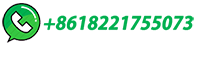
Microsoft Word
Research Triangle Park, North Carolina 27711 October 2010 . 2 Table of Contents ... Thermal Units (lb/MMBtu) for fuels combusted at cement kilns in the United States. 6 . Gas 1. cement . emissions. emissions cement, and 2 emissions cement . gas emissions from . emissions . cement. 3. .
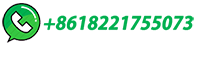
Everything you need to know about Cement Kiln Dust …
Cement kiln dust has also been used as a partial replacement for soda in the production of glass where color and high chemical stability are not essential considerations. High alkalies in CKD increase the rate of sulfate decomposition that is the main cause of ing in glass baths (Emer, 1969). A soda-kiln-dust glass has many similarities to ...
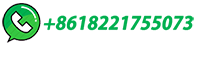
Giant Cement Company | About us
Giant was the first cement company in South Carolina. During its first year of production, 1949, Giant delivered 110,000 tons of cement to its customers. ... 1962, and 1974, including the installation of Kilns 2, 3, 4, and 5, as well as the installation of the first baghouse used on a wet kiln. ...
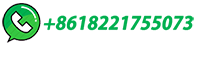
CEMEX Location Finder
View CEMEX USA Locations and locate a local sales team for CEMEX cement, aggregates, ready mix concrete and related products
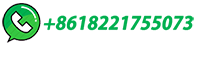
EVERY THING YOU NEED TO KNOW ABOUT HEAT …
EVERY THING YOU NEED TO KNOW ABOUT HEAT BALANCE IN CEMENT KILN . Before modem developmenls in kiln technology, there were efficient kiln operators that never had a complete understanding of …
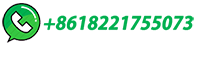
Geocycle USA
Geocycle recaptures and repurposes the resource value of many wastes through co-processing in cement kilns, including abrasives, baghouse dust, bauxite, bottom ash and fly ash, catalysts, ceramics, clay filters and sludges, FCC/spent catalyst, filter cakes, foundry sand and blast grit.
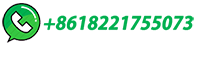
A clean approach through sustainable utilization of cement kiln …
The fresh cement kiln dust acts as alkali-bearing waste with high efficacy in the interaction with amorphous aluminosilicate within sludges, yielding hardened materials through what is known as pozzolanic reaction.
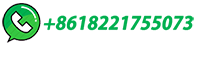
Tire Incineration | Energy Justice Network
At the end of 2003, 89 U.S. facilities burned TDF on a regular basis, about half of which (43) are cement kilns with the rest being pulp/paper mills (17), coal-fired power plants (13), and other industrial boilers or waste incinerators (15). ... The North Carolina Division of Pollution Prevention and Environmental Assistance, a government ...
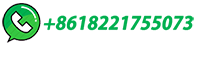
US EPA
All new cement kilns are this type primarily due to energy savings and greater throughput capacities compared to other kiln types. PH/PC kiln systems are so named because
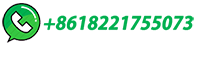
Giant Cement Company | Homepage
Giant Cement Company is a proud producer of top quality Portland and masonry cements. Located in Harleyville, South Carolina, Giant provides the materials for highways, …
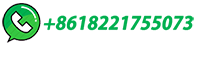
Coplay Cement Company Kilns | AMERICAN HERITAGE
The kilns were soon superseded by rotary kiln technology that required very little labor to operate. In 1904 the company shut down its vertical kilns and in the 1920s demolished the surrounding buildings and removed the upper 30 feet of the kilns. Lehigh County acquired the kilns in 1976 and launched a rehabilitation campaign.
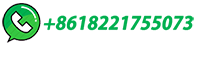
Cement Kilns: Kiln History
The cement kiln burns rawmix to produce clinker, which is then ground to make cement. The cement kiln is the heart of the cement making process: this is today almost a cliché, but was not always quite so true. In the modern cement plant, the kiln is the most expensive and technically complex part of the plant, and because it must be run all ...
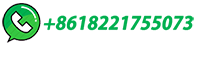
Cemex and MPP Collaborate to Accelerate Decarbonization …
The high heat required in cement production is a key challenge to decarbonizing the cement industry. Cemex and MPP are exploring technologies that can substitute fossil fuels traditionally used to heat kilns with waste, renewable gas, biomass, hydrogen, and electrification of the kilns as they strive for a more sustainable industrial …
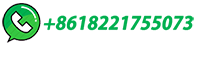