Gyratory VS Jaw Crushers: Advantages & Disadvantages
Routine maintenance and repair jobs are generally more easily accomplished on the jaw crusher than on the gyratory. Major repairs are about a stand-off. ... COMPARISON OF PRIMARY JAW AND GYRATORY CRUSHERS by Weiss, N. L., Society for Mining, Metallurgy & Exploration, Pages 4.
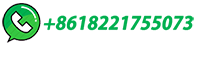
8 Tips for Crusher Safety | Stewart-Amos …
Ensure that operators keep detailed maintenance records that keep track of any issues with machinery. 2. Perform Regular Maintenance ... Types of primary crushers include jaw, cone, gyratory and impact crushers. …
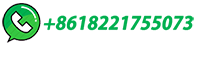
® C Series™ jaw crushers
® C Series™ jaw crushers are used as primary crushers in aggregates production, mining operations and recycling applications. ... Maintenance platform. Check the video You need to accept marketing …
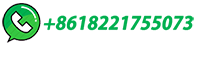
Jaw Crusher
Overview of size reduction of raw materials of the cement industry. Vipin Kant Singh, in The Science and Technology of Cement and Other Hydraulic Binders, 2023. 4.2.1 Jaw crushers. Jaw crushers are used for the primary reduction of hard and abrasive materials used for cement manufacture. Jaw crushers 3 are of either Blake-type or Dodge-type and operate by applying …
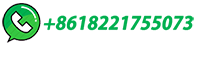
Jaw Crusher for Primary Crushing | Fote Machinery
A jaw crusher is important primary crushing equipment in the mining industry. Its parts, types, quality, and price are attractive to users. ... Regular maintenance of your jaw crusher is essential to ensure optimum performance and long service life. This includes checking worn parts, maintaining jaw plates, ensuring lubrication, tightening ...
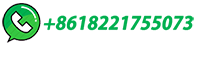
Jaw Crusher Working Principle
The jaw crusher discharge opening is the distance from the valley between corrugations on one jaw to the top of the mating corrugation on the other jaw. The crusher discharge opening governs the size of finished material produced by the crusher. Measuring Discharge Opening: Measure distance at bottom of jaws at the point of the crushing cycle …
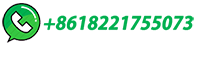
McLanahan | Jaw Crushers
McLanahan's Universal Jaw Crusher produces more spec material at a lower cost per ton and ensures continuous crushing action with less abrasive wear. ... Universal 3242 Jaw Crusher Portable Primary Jaw Plant. Blog What Type of Crusher Is Best for Primary Crushing? Webinars ... which leads to increased production and less downtime on maintenance.
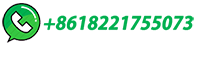
Types of Crushers Explained: Everything You Need to Know
Primary crushers are built to process large and abrasive feed materials. They can handle feed sizes of up to 1500 mm, but it depends on the type and size of the crusher. ... need more intricate foundation and have higher operating and maintenance costs as compared to jaw crushers. The decision of a jaw crusher or a gyratory crusher is based on ...
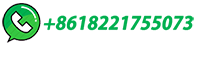
J-1160 Primary Mobile Jaw Crusher | Tracked Crusher | Finlay
The second generation Finlay J-1160 Primary Mobile Jaw Crusher was designed with the customer and operator in mind. The machine has been designed with increased under jaw clearance and all round preventative maintenance and serviceability access. The heartbeat of the machine is the renowned and aggressive 1000 x 600mm (40" x 24 ...
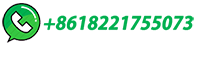
McLanahan | Best Practices for Feeding Jaw Crushers
Jaw Crushers are often used as primary crushers where the main duty is to produce a material that can be transported by belt conveyor to the subsequent stages of the plant. They crush material via compression, by …
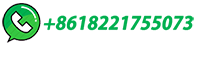
McLanahan | Best Practices for Feeding Jaw Crushers
Jaw Crushers are often used as primary crushers where the main duty is to produce a material that can be transported by belt conveyor to the subsequent stages of the plant. They crush material via compression, by squeezing it between a moving piece of steel and a stationary piece of steel. One of the main benefits of Jaw Crushers compared to other types …
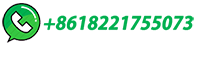
Understanding Types of Jaw Crusher: A …
Blake jaw crushers, also as double toggle jaw crushers, are characterized by the position of the pivot of the swing jaw, which is located at the top of the machine. This design allows for a larger feed size and a higher …
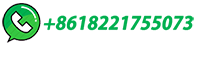
Primary Crushing Station | SpringerLink
Mobile primary crushing station generally includes crusher, feeding device, unloading device, maintenance system, walking mechanism, etc. The crushers used can be divided into jaw type, gyratory type, and so on. The combination of mobile primary crushing station and belt conveyor system can reduce the vehicle distance, save the mining cost ...
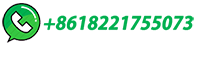
The Ultimate Guide to Jaw Crushing Machines: Types
Common Jaw Crusher Maintenance Issues and Solutions. Even with regular maintenance, jaw crushers may still experience some issues. Here are some common maintenance problems and solutions: Uneven wear of the jaw dies: This can be caused by incorrect feed material, excessive wear on the jaw plates, or a misalignment of the crushing …
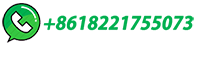
Everything you need to know about Crushers in Cement …
The single rotor used as primary crusher only. Jaw crushers. Jaw crushers are used for the primary reduction of very hard and abrasive admixtures for cement manufacture. The reciprocating motion of the crushing jaw of the double – toggle (or Black type) jaw crusher subjects the material to a mainly compressive action.
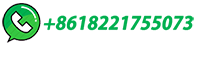
Jaw crusher EB | FL
Our Jaw Crusher EB series has a rugged and reliable design that's ideal for high capacities, while also offering low wear and tear and easy maintenance. The EB Pro series is especially suited to crushing medium hard to hard rock in quarries, ore mining industry, recycling industry and numerous other areas of the primary industry.
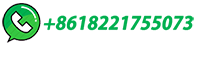
Construction Working and Maintenance of Crushers …
Bolts, shovel teeth, picks and other uncrushable metal that is often present in crusher input. As the term "primary" implies, primary crushers are used in the first stage of any size reduction cycle. Generally gyratory crushers, jaw crushers, high speed double roll crushers,
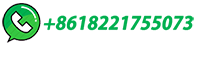
Below the surface: Setting up an underground …
Jaw crushers are the most common solution in underground applications when the throughput is below 1000 tonnes per hour, depending somewhat on the scalping solutions. Above 1000 tph, primary gyratory …
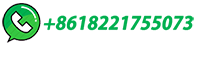
Understanding Jaw Crusher Parts and Their …
The size and shape of the fixed jaw also play a role in determining the capacity of the jaw crusher. Maintenance Tips: ... the proper tension on the toggle and providing a secure connection between the movable jaw and the …
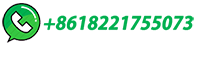
What Type of Crusher Is Best for Primary Crushing?
Types of Primary Crushers. There are several types of primary crushers, including: Gyratory Crushers Jaw Crushers Hammermills Horizontal Shaft Impact Crushers Sizers Roll Crushers Cone Crushers Feeder-Breakers Gyratory Crushers. Gyratory Crushers are an excellent choice for a primary crusher, as they can handle very hard and abrasive …
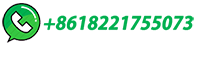
Jaw crusher spare parts and maintenance introduction
Jaw crushers are essential tools in the mining, construction, and aggregate industries, serving as primary crushers to break down large rocks into smaller, more manageable pieces. ... it's crucial to understand its structure, spare parts, and proper maintenance procedures. Jaw Crusher Structure: a jaw crusher consists of several key …
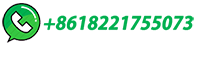
Primary Crusher Optimisation for Improved Comminution
the primary crusher. DEFINITION The primary crusher selection is the key to the success of any mining operation that involves the reduction in size of the ore. The crushing plant can be provided with almost any type of primary rock crusher. The rock/ore determines the type of crusher. The plant capacity determines the size of the crusher.
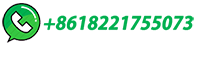
Jaw Crusher: Range, Working Principle, Application
Jaw Crushers are configured for primary crushing of even hardest rock. Our Jaw Crushers are crushing without rubbing Minimum dust Oil lubrication, devise having Oil/Grease lubrication system. The company crushers are designed for long life service with minimum maintenance for hard, tough, abrasive material and overload high capacity. The ...
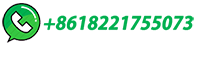
Influence of jaw crusher parameters on the quality of primary …
The part of aggregate processing investigated in this paper is the crushing, specifically primary crushing using a jaw crusher. Coarse aggregates for unbound use are often produced using a single crushing stage in a jaw crusher, as opposed to concrete or asphalt aggregates, where at least two and often three or four crushing stages are used ...
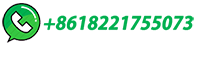
Primary Crushing: A Comprehensive Guide
Jaw crushers (types of compression crushers) efficiently reduce large rocks and materials through a compressive crushing action, with an input size capacity that can accommodate pieces as big as one meter (1000mm) in diameter. The output size from a jaw crusher can typically be adjusted between 150mm to 300mm, depending on the discharge …
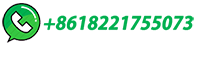
4 Types of Stone Crushers' Maintenance and …
The most practical jaw crusher repair and maintenance manual. Other ways to protect your jaw crusher parts. ... For example, if a horizontal shaft impact crusher is used in primary crushing, the rotor should be solid because …
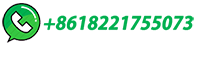
AMIT 135: Lesson 5 Crushing – Mining Mill Operator Training
The purpose of the primary crusher is to reduce the ROM ore to a size amenable for feeding the secondary crusher or the SAG mill grinding circuit. ... Can handle high abrasion with low maintenance. Jaw Crusher Disadvantages. Maximum capacity of 1,000 MTPH. Can be used for primary crushing only.
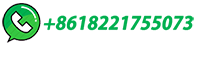
The Most Practical Jaw Crusher Repair and Maintenance …
A primary jaw crusher is a machine designed to reduce large rocks into smaller rocks, gravel, or rock dust. It is used in many industries, including mining, construction, and demolition, to crush materials such as …
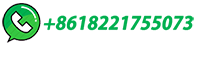
The Ultimate Guide to Jaw Crushing Machines: …
A hydraulic jaw crusher is a type of jaw crusher that uses hydraulic pressure to crush materials. It has a movable jaw that is operated by an eccentric shaft, as well as a fixed jaw that is positioned opposite the movable …
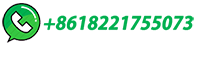
What is a Jaw Crusher and Selecting the Right One
Jaw crushers feature safe, simple operation and maintenance. Disadvantages of a Jaw Crusher. Jaw crushers can also have some disadvantages compared to other types of size reduction. Opposing jaw plates are less efficient at reducing materials that are tough, ductile, or soft instead of hard and brittle.
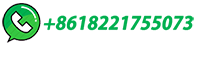