Copper Recovery from Yulong Complex Copper Oxide Ore by Flotation …
A combined process of flotation and high-gradient magnetic separation was proposed to utilize Yulong complex copper oxide ore. The effects of particle size, activators, Na2S dosage, LA (a mixture of ammonium sulfate and ethylenediamine) dosage, activating time, collectors, COC (a combination collector of modified hydroxyl oxime acid …
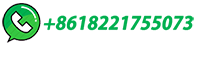
Effect of electroflotation on quartz and magnetite and its …
The most effective technologies for the beneficiation of iron quartzite are wet magnetic separation in low intensity magnetic field and reverse flotation of quartz. Removing quartz from iron ore is of great importance because it represents one of the most common gangue minerals in iron ores.
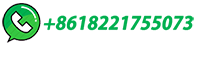
Comparison Of Limonite Gravity, Magnetic And Flotation Separation
Gravity separation, magnetic separation and flotation are the most widely used limonite beneficiation methods. Each technique has unique advantages and limitations, so it is critical to understand their differences and choose the most suitable method to maximize the recovery of valuable iron from limonite ore.
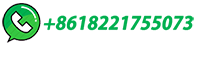
The Use of Flotation and High-Intensity Magnetic Separation …
This paper discusses the possibilities for lowering feldspar ore's titanium and iron content to make it suitable for industrial use. The feed sample of (-250+38~mu) m was subjected to comminution, desliming, attrition, and flotation procedures prior to magnetic separation as part of earlier separation processes by [].Figure 2 depicts the …
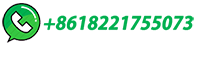
Flotation of Iron Ores: A Review
ABSTRACT A tremendous amount of research has been done on refining the flotation process for iron ore and designing the reagents which go into it. This paper …
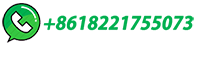
Chrome Ore Process Plant
Moreover, the magnetic separation process has no pollution to the environment, the chrome ore magnetic separation technology has been popularized and applied in the major mineral processing plants. Usually the chrome ore through gravity separation, and after the screening, the slurry is sent to a flotation cell or magnetic separator.
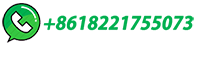
An overview of the beneficiation of iron ores via reverse …
Despite the recent success of the reverse anionic flotation of iron ores in the Anshan province in China, reverse cationic flotation remains the most popular flotation route used in the iron ore industry (Ma, 2012a)paring reverse anionic and cationic flotation is difficult because the processes are governed by the chemical, physical and …
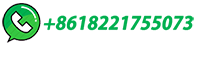
(PDF) Flotation of Iron Ores: A Review
A novel stepped flotation technique is discussed for the treatment of carbonate-rich iron ores. The necessity of desliming to enable effective flotation is …
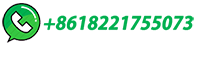
Developments in the physical separation of iron ore: Magnetic …
This chapter introduces the principle of how low-grade iron ores are upgraded to high-quality iron ore concentrates by magnetic separation. Magnetite is the most magnetic of all the naturally ...
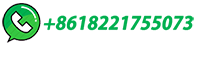
Physical separation of iron ore: magnetic separation
Abstract This chapter introduces the principle of how low-grade iron ores are upgraded to high quality iron ore concentrates by magnetic separation. Magnetite is the most magnetic of all the naturally occurring minerals on earth and can be readily …
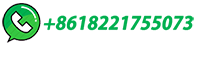
iron ore-MECRU
Iron ore is an important raw material for iron and steel production enterprises. Natural ore (iron ore) gradually selects iron through procedures such as crushing, grinding, magnetic separation, flotation, and gravity separation. Iron ore is a mineral aggregate that contains iron element or iron compound and can be used economically.
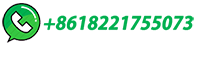
Improving recovery of iron using column flotation of iron ore …
In general, the industrial flowsheets for the beneficiation of itabirite iron ores from the Quadrilátero Ferrífero (Minas Gerais state) in Brazil involves grinding, desliming, magnetic separation and cationic reverse flotation using both mechanical and columns flotation cells. At Brazilian plants, it is estimated that Fe losses generated at the slimes …
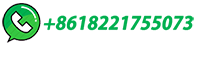
Flotation Froth
In addition to the two primary flotation agents there are also a number of modifying and conditioning reagents, which control a variety of ore and flotation circuit variables [13]. For instance, lime is a depressant for pyrite (FeS2) in the …
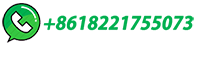
Study on Magnetic Separation-Reverse Flotation Tests of the …
The iron content of an iron ore from Anshan is 32.19%. The iron minerals are mainly magnetite and hematite. The gangue minerals mainly include quartz. For this …
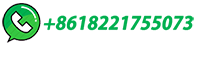
Transforming iron ore processing – Simplifying the …
This work describes the concentration of iron ore slimes on a pilot scale by using a 500-mm diameter flotation column and a novel collector, which renders the use of a depressant unnecessary.
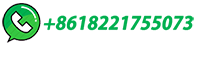
Flotation of Iron Ores: A Review
While flotation is often more expensive than magnetic separation, flotation also recovers the non-magnetic iron ore ... flotation cells and were eventually removed. ... The flotation of iron ore ...
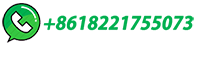
Collecting Agent–Mineral Interactions in the Reverse Flotation of Iron
Froth flotation has been widely used in upgrading iron ores. Iron ore flotation can be performed in two technical routes: direct flotation of iron oxides and reverse flotation of gangue minerals with depression of iron oxides. Nowadays, reverse flotation is the most commonly used route in iron ore flotation. This review is focused …
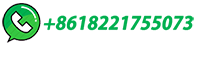
gravity separation examples, gravity separator, magnetic …
Iron Sand Processing Plant is applicable for wet magnetic separation of materials such as magnetite, pyrrhotite, roasted ore and ilmenite whose size is less than 3 mm and also used for iron removal operation of materials such as coal, nonmetalliferous ore and construction material and so on.
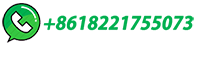
Recovery of phosphorite from coarse particle magnetic ore by flotation
The Fe 3 O 4 in iron ore with phosphorus is recovered by magnetic separation and the P 2 O 5 is recovered from the tailings of magnetic separation by flotation (Tang et al., 2012). In this way, iron and phosphorus resources could be comprehensively used (Hernáinz et al., 2004, Sis and Chander, 2003).
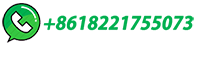
Enhanced Iron Recovery from Ultrafine Iron Ore Tailing
The newly designed beneficiation circuit involves iron ore tailing processing in different stages, i.e., de-sliming and gravity separation, followed by magnetic separation. Further, the results of the conventional process, i.e., de-sliming followed by flotation using dual extraction column flotation cell, have been compared with the …
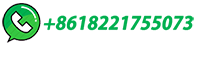
ball mill,spiral classifier,flotation cell,magnetic …
Henan Fote Heavy Machinery Co., Ltd.is a professional manufacturer and exporter specilized in the prodution of ball mill, magnetic separator, rubble-tyred mobile crushing station, dryer, jaw crusher, Rotary kiln and …
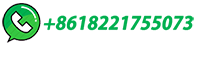
The Desulfurization of Magnetite Ore by Flotation with …
problem in iron ore smelting process. However, the magnetic separation of pyrrhotite from magnetite is problematic, due to their similar magnetic property and magnetic flocculation between pyrrhotite and magnetite [3]. Flotation has been commercially used as a method for removing pyrrhotite from magnetite for high sulfurous iron ores [4].
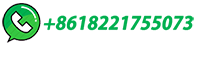
ball mill,spiral classifier,flotation cell,magnetic separator…
Henan Fote Heavy Machinery Co., Ltd.is a professional manufacturer and exporter specilized in the prodution of ball mill, magnetic separator, rubble-tyred mobile crushing station, dryer, jaw crusher, Rotary kiln and other large mining machinery equipment.
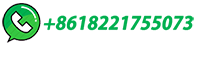
Beneficiation of Iron Ore Fines by Conventional …
netic Separation (L1MS),Medium Intensity Magnetic Separation (MIMS) and High Gradient Magnetic Separation (HGMS) are in-adequate to address the problems associated with fines and in-terlocked particles. Flotation is the most suitable technique for the selective separation of iron ore fines from gangue minerals, Direct flotation of iron …
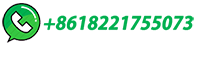
Flotation-magnetic separation for the beneficiation of rare …
The traditional beneficiation processes used including the combined gravity-magnetic-flotation process, dry magnetic separation, and heated flotation have been applied in the plant, resulting in terrible working conditions, elevated production costs, and a lowered beneficiation index, with a 50% average REO content in concentrate and 20% …
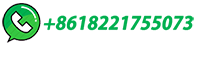
Iron Oxide Ore Mineralogy and Its Plant Flotation Circuits …
Mining operations usually provide ore of varying characteristics. At the Donganshan Sintering Plant, the ore is a low-grade, complex, hard-to-separate carbonate containing iron ore, and a two-step flotation circuit was previously developed to overcome the negative impact of the carbonates on the reverse flotation process. However, with …
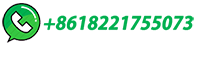
Transforming iron ore processing
In the recent past, iron ore resources from Brazil consisted of relatively high-grade iron ore, commonly processed via multi-stage crushing/screening, gravimetric concentration, magnetic separation, and reverse flotation. However, the high-grade iron ore reserves are in decline, resulting in the need to process the lower grade itabirite iron …
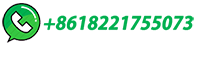
Separations | Free Full-Text | Application of Magnetic Separation
This paper summarizes the application of magnetic separation technology for resource utilization and environmental treatment in different fields, such as non-metal decomposition, valuable metal recovery, use of magnetic carrier chemical separation, biomedical targeted magnetic separation, and use of magnetic species separation in …
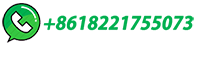
(PDF) An overview of the beneficiation of iron ores via …
Research regarding iron ore flotation began in 1931, demonstrating that reverse cationic flotation is a very efficient method for beneficiating oxidised iron ores. ... magnetic separation improved ...
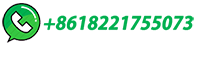
Experimental Study on Iron Recovery from Flotation Tailings …
The flotation tailings of the Donganshan sintering plant contain 22.82% Fe, 9.87% FeO, 51.24% SiO 2 and a low S and P content of 0.03%, which belongs to low sulphur, low phosphorus and high silicon type iron tailings. ... on iron recovery from flotation tailings of Donganshan iron ore by combined magnetic separation and flotation process[J ...
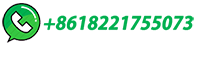