Iron Ore – Minecraft Wiki
Iron ore is a mineral block found underground. It is a source of raw iron, which can be smelted into iron ingots. Deepslate iron ore is a variant of iron ore that can generate in deepslate and tuff blobs. Iron ore itself can be obtained by mining it with a stone pickaxe or higher enchanted with Silk Touch. When mined without Silk Touch, iron ore drops raw iron. It is affected by the …
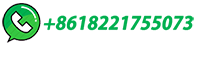
Global iron and steel plant CO2 emissions and carbon …
We find that, in 2019, up to 74.5% (1,389.1 Mt) of the total crude steel produced come from coal-based iron and steel plants. Specifically, coal-based blast furnace-basic oxygen furnace (BF-BOF ...
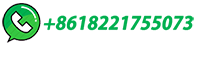
The six main steps of iron ore processing
When iron ore is extracted from a mine, it must undergo several processing stages. Six steps to process iron ore. 1. Screening We recommend that you begin by screening the iron ore to separate fine particles below the crusher's …
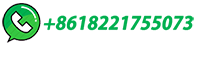
Energy consumption in smelting reduction (SR) processes
In contrast, conventional processes use coke and hematite/sinter in the blast furnace, in SR processes, other alternative fuels and iron ore sources, like charcoal and fine iron ores, can be used ...
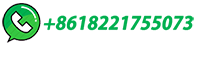
Chinese-built steel plant in Zimbabwe fires up its furnace as …
A new US$1.5 billion Chinese-built iron and steel plant in Zimbabwe has fired up its blast furnace as it begins production of pig iron, a major raw material needed to make steel. There are high ...
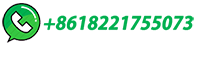
HIGHVELD STEEL PROSPECTUS: IRON PLANT 1
• The purchase of Iron making Plant 1 has the following distinct advantages: • The Flexibility of equipment: The newly upgraded Open Slag Bath has a proven track record of producing a range of products including ferroalloys. • Open Slag Bath and pre-heating technology: Inherent to the design of the plant is the ability to process large amount of fine material which are problematic …
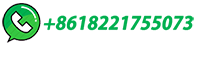
Smelting Reduction Processes | SpringerLink
In SR processes, iron ore and coal are added directly to a metal-slag phase where the ore is reduced. The SR process combines the gasification of coal with the smelting reduction of iron ore. Energy consumption of smelting reduction is lower than that of blast furnace, as coking step is avoided and the need for ore preparation is reduced.
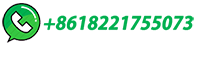
Iron processing
Iron processing - Smelting, Refining, Alloying: The primary objective of iron making is to release iron from chemical combination with oxygen, and, since the blast furnace is much the most efficient process, it receives the most attention here. Alternative methods known as direct reduction are used in over a score of countries, but less than 5 percent of iron is made this way.
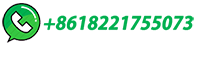
Iron processing | Definition, History, Steps, Uses, & Facts
Learn about the key stages in iron ore processing, including crushing, screening, and beneficiation techniques for optimal resource utilization. +86 ; ... A Step-by-Step Approach to Setting Up a Spodumene …
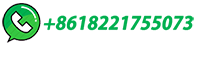
UGANDA OPENS $200M IRON ORE SMELTING PLANT
Ekeomah Atuonwu. Uganda has opened a $200 million iron ore smelting plant, which will help the region reduce its reliance on scrap metal, billets, and coils for raw materials.. Tembo Steels Uganda Ltd is building a facility in Iganga, eastern Uganda, with a capacity to produce 1.2 million tonnes of metal per year. "This is East Africa's largest integrated steel mill …
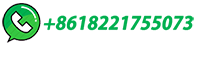
Iron Making in Mini Blast Furnace (MBF)
The products from mini blast furnaces are of the same quality as that of normal Blast Furnaces and are free of tramp elements - this is of particular advantage in steel making in mini steel plants. Use of 40 - 45% hot metal in EAF (Electric …
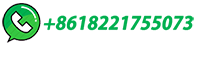
The Smelting Industry: Global Importance And Risks
Primary smelting processes the mine ore and concentrates, and secondary smelting processes recover the scraps. 4. History of Smelting. The 14th Century is when smelting first began to be practiced in Europe. At that time, the blast furnace was introduced, which used greater air volumes, and layered the iron ore with charcoal, according to Jays ...
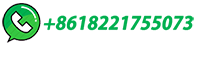
OM Holdings | A Manganese Ore & Ferroalloy Company
Smelting is the process of converting raw ores mined from the ground into alloys used in a variety of industrial applications. The plant has a production capacity of 120,000-126,000 metric tonnes per annum of ferrosilicon (FeSi), 333,000-400,000 metric tonnes per annum of manganese alloys alloys and 21,000 to 24,500 metric tonnes per annum of ...
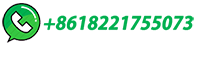
Alternative emerging ironmaking technologies for energy …
Smelting reduction processes avoid this energy use because they make iron directly from iron ore and coal, omitting the need for coke ovens and sinter plants. The …
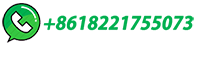
From Ore to Iron with Smelting and Direct Iron Reduction
Mini mills, Micro mills, Nano mills and the Energy Saving …
The micro mill has a design capacity of 300,000 short t/yr (272,000 metric) of finished product with a 35 short ton tap weight melt shop intended to work with scrap charge. The plant …
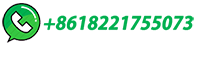
Iron Ore
An Ice Pip Fish Pond can produce 5 Iron Ore when the population of the pond reaches 3. Can be purchased from Clint's shop at the Desert Festival for 4 Calico Eggs each. Smelting. Iron ore can be smelted in a Furnace to create an Iron Bar. The smelting requires 5 iron ore and 1 coal to begin and takes 2 in-game hours to complete. Crafting
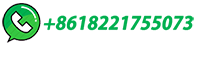
The production of pig iron from crushing plant waste using hot …
With low iron content degree (Fe < 56%), Fe content degree improvement process is required for this iron ore waste to be able to use as feed material in smelting process into pig iron. Pig iron is a solid form of hot metal, obtained from iron ore or scrap recycling, and it is processed with blast furnace or electric arc furnace.
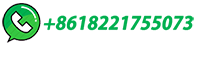
Mini mills, Micro mills, Nano mills and the Energy Saving …
1.0Mt/yr steel plant. Danieli, as a plant designer and builder, is at the forefront of this trend. MINI MILLS World electric steelmaking has increased from 595Mt in 1960 to 1,606Mt in 2013, an increase of 170%. Since their early beginnings in the 1970s, mini mills have gradually grown in size to capture the economies of scale and have
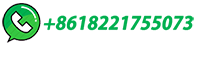
Iron ore plant in Silver Bay celebrates $100 million …
HBI plants turn pellets into "low-silica" iron bricks that then get converted into steel by the mini-mills or electric arc furnaces (EAFs) that have become the most common method of steelmaking ...
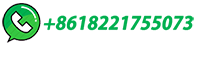
COREX® — SMELTING REDUCTION PROCESS
Corex, the unique smelting-reduction process allows for the cost-effective and environmentally friendly production of hot metal from iron ore and coal. In the Corex process, all metallurgical work is carried out in two separate process …
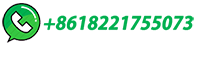
Smelting and Selective Reduction of Limonitic Laterite Ore in Mini …
This study aims to study the smelting process of limonitic laterite nickel ore. The smelting process was performed using a Mini Blast Furnace pilot plant with a capacity of ten tons of ore per day or 350 kg per batch. ... the crude ferronickel or nickel pig iron products and the resulting slag were characterized using EDX and XRD. As a result ...
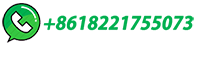
Iron Making: Smelting
The blast furnace was where the smelting process was started. NPS Photo / Elizabeth Thakkar. In 1646, the original blast furnace roared to life, lit with a 3000 degree fire that was kept burning 24 hours a day for months at a time. ... Gradually at first, charcoal, iron ore, and gabbro were charged into the top of the furnace in layers by the ...
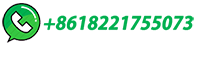
Uganda opens $200m iron ore smelting plant
Uganda has commissioned a $200-million iron ore smelting plant that could significantly reduce the region's heavy dependence on scrap metal, billets and coils for raw material. The plant in Iganga, eastern Uganda, with a capacity to process 1.2 million tonnes of metal annually, is a project of Tembo Steels Uganda Ltd. ...
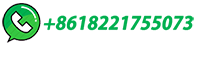
Smelting of High-Carbon Ferrochrome from Prereduced …
Experimental smelting of three batches of prereduced chromite raw materials with different degrees of metallization of chromium was conducted in the 0.2 MVA ore-smelting furnace of the Chemical and Metallurgical Institute named after Zh. Abishev (Karaganda). To assess the performance indicators of the remelting of prereduced chromite raw materials in …
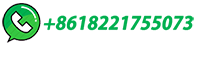
Evolution of Ironmaking Techniques | From …
As societies progressed, humans began to extract iron from terrestrial sources, marking the transition from the use of meteoric iron to smelting iron ore. One of the earliest known methods of iron smelting was the bloomery process. This …
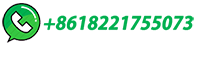
What is Smelting
1. Iron. Primary Metal for Smelting: Iron is the primary and most commonly used metal in the process of smelting. Its versatility and abundance make it important for metallurgy. Steel Production: Iron ore is the raw material for steel production. In the smelting process, iron ore is heated, leading to the separation of iron from impurities ...
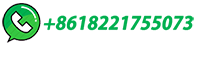
Recycling of steel plant mill scale via iron ore
Mill scale is an iron oxide waste generated during steelmaking, casting and rolling. Total generation of mill scale at JSWSL is around 150 t/day and contains 60–70%FeO and 30–35%Fe2O3.
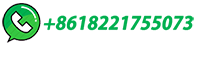
Alternative emerging ironmaking technologies for energy …
Smelting reduction processes avoid this energy use because they make iron directly from iron ore and coal, omitting the need for coke ovens and sinter plants. The cyclone converter furnace consists of a cyclone for pre-reduction of the iron ore; the cyclone is mounted on a converter-type vessel in which the iron ore is then reduced to iron [20] .
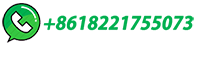
Iron processing | Definition, History, Steps, Uses, & Facts
Iron processing, use of a smelting process to turn the ore into a form from which products can be fashioned. Included in this article also is a discussion of the mining of iron and of its preparation for smelting. Iron (Fe) is a relatively dense …
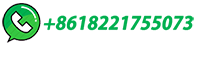
Uganda opens $200m iron ore smelting plant | Radarr Africa
Uganda has commissioned a $200 million iron ore smelting plant, which will help the region reduce its reliance on scrap metal, billets, and coils for raw materials. Tembo Steels Uganda Ltd is building a facility in Iganga, eastern Uganda, with a capacity to produce 1.2 million tonnes of metal per year. Sanjay Awasthi, chairman of
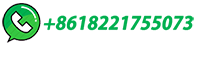