Flotation of Iron Ores: A Review
Overview of the Groveland Mine iron ore beneficiation process, utilizing direct flotation in acidic conditions (based on Houot 1983). Figure 3. Overview of the iron ore beneficiation process in ...
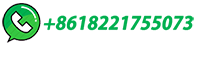
The beneficiation of lithium minerals from hard rock ores: …
There are two economic sources of lithium; brines and hard rock ores. The majority of the global lithium production, greater than 60%, is produced from brines while lithium ores accounted for the remaining production (Ebensperger et al., 2005).Table 1 summarises the world's major lithium producers from ores and brines, and the total reserves. The lithium …
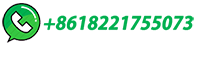
Some opportunities to increase performance of tailing …
therefore, control thickener design within the specified process requirements [15]. The Gol-E-Gohar Iron Complex located in the south of Iran, is one of the largest Iron ore concentrate …
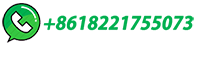
How to Extract Iron from Hematite: Methods and …
Medium-grained hematite refers to iron ore with an embedded particle size between 0.02 and 2mm. This type of hematite is also relatively easy to select, mainly using gravity separation, magnetic separation and magnetic …
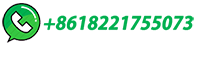
Iron Ore – Beneficiation & Pelletization Division
Businesses Home > Our Businesses overview > Manufacturing > Iron Ore – Beneficiation & Pelletization Division > Iron Ore Beneficiation & Pelletization (IoBP) Overview Products Technology Location Overview Essel Mining and Industries Limited (EMIL) is a pioneer in manufacturing of iron pellets through the distinguished and most compact circular Pelletization …
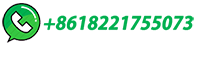
shibang/sbm what is a thickener iron fines benefeciation.md …
You can not select more than 25 topics Topics must start with a letter or number, can include dashes ('-') and can be up to 35 characters long.
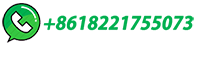
Advancing Iron Ore Beneficiation: Exploring Cutting-Edge
The evolution of iron ore beneficiation process technology underscores the industry's commitment to innovation and sustainability, driving continuous improvement in ore processing efficiency and ...
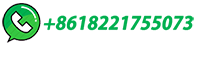
Iron ore tailings valorization through separate
In iron ore processing plants, different tailing streams are usually transferred to the tailings thickener for partial dewatering and finally transferred to the tailings dam as a single stream. Therefore, the mixing of different tailings streams happens. This way can challenge the process of reprocessing the tailings in the tailings dam since the mixing of different tailings …
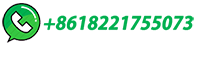
Studies on the effect of flocculant adsorption on the …
The iron ore beneficiation circuits mostly consist of different combinations of unit operations such as gravity separation, magnetic separation, and flotation process. Most of the beneficiation circuits are wet process. Thickener and filtration units are typically used for dewatering. Most of the water of the process is associated with the ...
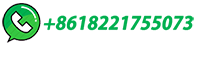
Various Types Of Iron Ore Beneficiation Processes
iron ore contain high sulfur, phosphorus Beneficiation. The common processes used to remove sulfur from iron ore concentrates are flotation and roasting. At the same time, the latter is costly and produces …
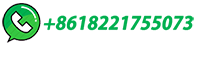
Beneficiation Strategies for Removal of Silica and
It covers different types of collecting agents used in reverse iron ore flotation, the surface characteristics of minerals commonly present in iron ores (e.g., iron oxides, quartz, alumina-bearing ...
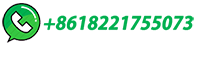
Improving flocculation and dewatering performance of iron …
Iron ore is a fundamental pillar in construction globally, however, its process is highly polluting and deposits are becoming less concentrated, making reusing or reprocessing its sources a ...
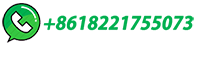
Development of process for beneficiation of low-grade …
tion of low-grade iron ore using conventional processes is a challenging task, and interesting research work is in progress (Dey et al., 2012.; Suthers et al., 2014; Li et al., 2009) Some recent practices for the beneficiation of low-grade iron ores by different companies are shown in Table 2.
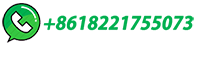
Minerals | Free Full-Text | Exploring Low-Grade Iron Ore …
The beneficiation of low-grade iron ores is a key research and development topic in the mineral processing industry. The gradual exhaustion of high-grade iron ore reserves, …
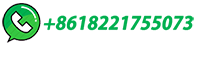
Beneficiation Strategies for Removal of Silica and Alumina …
Minor sections of this work were presented at Iron Ore 2021 (Nunna et al. 2021b), but the work therein has been significantly expanded upon. A number of references have been given in this paper to Iron ore: Mineralogy, processing and environmental sustainability, ed. L. Lu. Cambridge: Woodhead Publishing. A second edition of this book is in ...
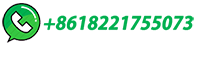
Iron (Fe) Ore | Minerals, Occurrence » Geology Science
Description and properties of common iron ore minerals. Iron ore minerals are rocks or minerals that contain iron in concentrations high enough to be economically extracted. Common iron ore minerals include: Hematite (Fe2O3): Hematite is the most abundant and important iron ore mineral. It is typically steel-gray to black in color and has a metallic luster.
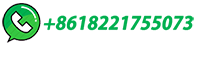
Iron ore tailings valorization through separate
In iron ore processing plants, different tailing streams are usually transferred to the tailings thickener for partial dewatering and finally transferred to the tailings dam as a …
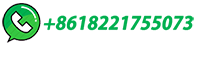
Iron Ore Processing: From Extraction to …
The final stage in iron ore processing is ironmaking, where the iron ore is transformed into molten iron through a process called reduction. The most common method of ironmaking is the blast furnace route. In a blast …
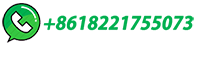
Chrome ore beneficiation challenges & opportunities – A review
Three different sorbent-to-chromite mass ratios, namely 0.5:1, 1:1, and 2:1, were tested with different process conditions, including dewatering in a stationary and a rotatingl bed.
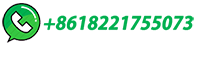
Niobium-Tantalum Ore Beneficiation
The chemical formula of niobium-iron ore-tantalite is AB 2 O 6, both of which are referred to as niobium-tantalum. Where A in the formula stands for iron and manganese, and B stands for niobium and tantalum. The magnetization rate of niobium-iron ore-tantalite is (22.1 to 37.2) × 10-6. The dielectric coefficient of niobium-iron ore is 10 to 12 ...
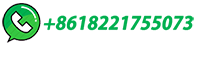
Processes for Beneficiation of Iron Ores – IspatGuru
The iron ores that fall within these three categories have quite different processing requirements. ... Generally, tailings proceed to a thickener prior to going to a tailings impoundment. ... beneficiation than simple washing and is used on the more hard ores that require crushing to break up the gangue rich layers. Jigs used for iron ore ...
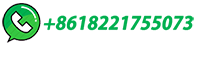
Some opportunities to increase performance of tailing …
therefore, control thickener design within the specified process requirements [15]. The Gol-E-Gohar Iron Complex located in the south of Iran, is one of the largest Iron ore concentrate producers of this country. In this complex, in wet Iron ore processing plants, slurry thickeners are used to recycle water of tailings slurry.
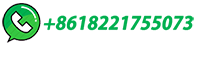
Physical separation of iron ore: magnetic separation
The magnetic thickener is often used for dewatering magnetite slurry after the separation procedure. It can also reject some of the light and fine nonmagnetic minerals. ... magnetic separation should always be given priority when designing iron ore beneficiation flow sheets. For some oxidized iron ores, the selectivity of high intensity and ...
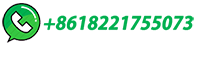
Synoptic view on P ore beneficiation techniques
The fixation of P-value in calcareous soil is commonly managed by adding phosphatase fertilizers manufactured by employing different natural P resources [6], [7], [8]. Phosphorite is the best-known natural ore having up to 13% P contents which have been used for the production of phosphatase fertilizers for a long [9], [10], [11]. Other P ...
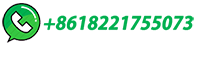
Advanced Analytics for Mineral Processing | SpringerLink
The optimal deep learning model consisted of five hidden layers for the DNN predicting the ore production and four hidden layers for the DNN predicting the crusher utilization, each with 40 hidden neurons [].The developed final deep learning model was evaluated for its ore production and crusher utilization prediction performance over ten days at the mine.
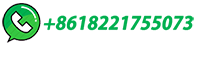
Coal beneficiation: theory and practice
The rock layers on top of a coal bed are called "overburden." The rock layers between coal beds are called "interburden." The rock layers below a coal bed are called "floor rock." Coal is comprised of three major maceral groups—vitrinite, inertinite, and liptinite—which proceeded along distinctly different metamorphic paths.
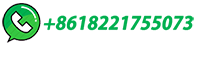
World leader in fine iron ore beneficiation
No one knows fine iron ore beneficiation like we do. From Canada's Labrador Trough region to India, Brazil, Africa and Australia's iron rich Pilbara, our expert teams deliver unrivaled expertise in fine iron ore beneficiation across the project lifecycle. Magnetic beneficiation of fine iron ore, Brazil YOUR IRON ORE BENEFICIATION SOLUTIONS 3 |
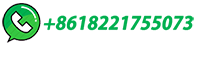
Thickener
3. High-Efficiency Thickener. In addition to the inclined plate installed in the thickener, the high-efficiency thickener has a special flocculant adding mechanism. The diameter of the thickener can be reduced to 1 / 3-1 / 2 of that of the common thickener, and the floor area is only 1 / 9-1 / 4 of that of the common thickener.
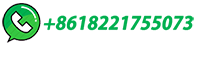
Beneficiation of Low-Grade Hematite Iron Ore …
Present investigation includes the magnetizing roasting of low-grade iron ore fines followed by grinding and beneficiation using magnetic separation. The hematite iron ore used in the investigation contains 53.17% T …
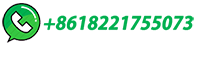
Collecting Agent–Mineral Interactions in the Reverse Flotation of Iron
Froth flotation has been widely used in upgrading iron ores. Iron ore flotation can be performed in two technical routes: direct flotation of iron oxides and reverse flotation of gangue minerals with depression of iron oxides. Nowadays, reverse flotation is the most commonly used route in iron ore flotation. This review is focused on the reverse flotation of iron ores, …
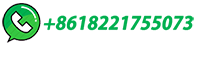