The Stages of Rock Crushing | Mellott
Understanding the different stages of rock crushing is essential so that your projects run smoothly. Learn more from Mellott.
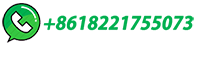
Modern controls, system integrator automate rock crushing
The manual system consisted of large start-stop pushbutton stations, and each of the 50 motors had its own hardwired switch. Control remained manual for about seven years until discussions started about modernizing the processes. This included equipment on both the dry and wet sides of the process, and later the clarifier.
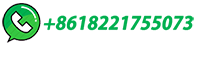
(PDF) An experimental investigation on rock crushability
Crushing is a size reduction process that plays a key role in both mineral processing and crushing–screening plant design. Investigations on rock crushability have become an important issue in ...
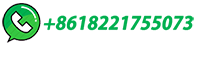
Standard Permit for Rock and Concrete Crushers: Learning …
Learn more about following our progress and your options for participating as we review applications for plants authorized under the Air Quality Standard Permit for rock and concrete crushers. Find out how these plants operate and how this permit calls for the plant's operators to keep dust and soot under control.
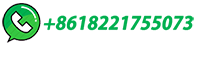
HS-SP-12-01 Crushing and sceener operations
Description of task: To remove material (rocks & dirt), transform it to produce specific material (aggregate) to different specced sizes. Load the crusher with an excavator or …
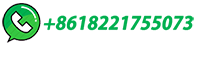
Rock Crushers & Pulverizers | Williams Crusher
Many processing plants or rock crushing plants utilize several rock crushing stations to accommodate different material sizes and requirement. Rock Crusher Applications. Williams' range of rock crushers makes them applicable across a variety of industries for many different types of rock.
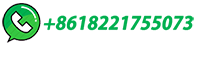
Crushing Plant Design and Layout Considerations
1 Crushing Plant Design and Layout Considerations Ken Boyd, Manager, Material Handling, AMEC Mining & Metals, Vancouver, BC ABSTRACT In mining operations, the layout of crushing plants and ancillary equipment and structures is a
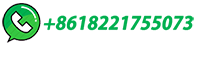
rock crushing process documentation
A process for reducing rocks and concentrating heavy minerals. To obtain minerals suitable for agedating and other analyses, it is necessary to first reduce the mineralbearing rock to a fine, sandlike consistency.
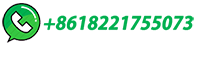
A dynamic ball compression test for understanding rock crushing
A split Hopkinson pressure bar system in combination with high speed cameras is utilized in the dynamic ball compression test, in which the spherical rock sample is adopted to avoid the shape effect and the relations between the loading rate and the fragmentation parameters are established. During crushing, rock particles are …
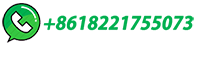
Rock Crushing Machines
For centuries, extracting valuable minerals and aggregates from the Earth has relied heavily on manual labour and primitive tools. However, in recent years, technological advances in rock crushing machines have transformed the way these industries operate, making the extraction process more efficient, cost-effective, and environmentally ...
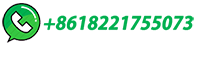
FactSheet
Using crushing machines at construction sites to reduce the size of large rocks, concrete, or construction rubble can generate respirable crystalline silica dust. When inhaled, the small particles of silica can irreversibly damage the lungs.
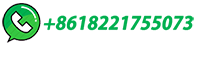
Rock Crushing Equipment | Rock Crushers | Kemper …
If you are a rock, sand, gravel, or mineral processing industry veteran, you know that several different types and styles of crushing equipment are used at crushing and screening plants.
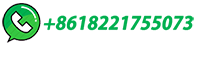
Mineral processing | Metallurgy, Crushing & Grinding
Mineral processing, art of treating crude ores and mineral products in order to separate the valuable minerals from the waste rock, or gangue. It is the first process that most ores undergo after mining in order to provide a more concentrated material for the procedures of extractive metallurgy.
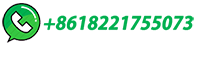
CRUSHING SCREENING
The screening process is just as important as the crushing itself. As the heart of every rock processing plant, screens are used to clas-sify materials in different stages of the crushing process as well as in final product separation. Designed as a …
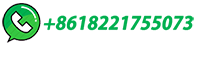
The Complete Guide to Primary Crushing, Secondary Crushing…
Learn everything you need to know about primary crushing, secondary crushing, and tertiary crushing in this comprehensive guide. Discover the types of crushers used in each stage, their working principles, and the advantages and disadvantages of each process. Get answers to frequently asked questions and …
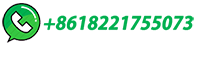
How 's Automation Systems Are Changing Rock Crushing
These smart systems are optimizing crushing operations, increasing production, reducing costs, and transforming the way the industry works. 's Automation Technology. At the heart of 's automation systems are advanced sensors and controls that automate key parts of the rock-crushing process. These include:
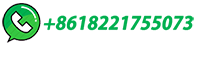
New Rules for Rock Crushing Plants
What emission limits apply to rock crushing plants? For rock crushing plants that fall below the capacity thresholds listed above, the visible emissions limit is 20% opacity, averaged over a continuous six-minute period.
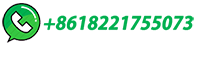
RockMax & SandMax VSI Crushers
2 The REMco Autogenetic Crushing Process Typical RockMax Coarse Rotor / Coarse Chamber Typical SandMax Fine Rotor / Fine Chamber ROCK-ON-ROCK reduction of all material feeds is achieved by high velocity energy transfer which commences
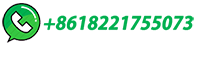
Measurement-Control for Crushing and Screening Process
It mainly includes crushing process control, crushing appliance fault diagnosis, and automatic distributing control. Crushing Process Control. To ensure the continuous, stable, and safe operation of the ore crushing production process, it is necessary to monitor the running state and parameters of key equipment (such as …
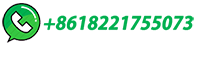
Rock Crusher Conveyor Belt Efficiency Guide
A rock crusher conveyor belt is an integral part of the rock crushing process. It serves as a critical link between various equipment, including crushers, feeders, and screens, facilitating a continuous and automated production flow. ... optimizing productivity and reducing manual handling. Rock crusher conveyor belts come in …
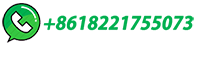
HS-SP-12-01 Crushing and sceener operations
%PDF-1.6 %âãÏÓ 59 0 obj > endobj 86 0 obj >stream application/pdf Sergio Suarez HS-SP-12-01 Crushing and sceener operations T21:35:40Z Word T14:37:22-07:00 T14:37:22-07:00 Mac OS X 10.10.5 Quartz PDFContext uuid:45c313fd-5c4f-6649-87dd-d4c857a9a1eb uuid:818b4c52-a3d9-6d4c-908d …
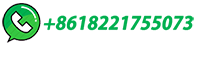
Artificial Sand Manufacturing Process
There are mainly three steps of crushing, washing and screening in the artificial sand manufacturing process. The crusher machines of the crushing step may employ use jaw crusher, impact …
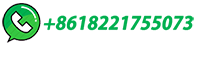
Crushing in Mineral Processing
Crushing is the process of reducing the size of materials so that they can be further processed, the crushing process usually include 3 stages: primary crushing, secondary crushing, and the tertiary crushing.
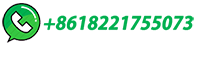
Crushing and Screening Handbook
Process simulation technology The computerized "Bruno" process calcula-tion system has already become the proven standard in the crushing industry. Rock qual-ity, feed …
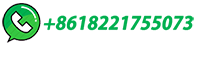
Site safety and safer aggregate crushing operations
There are many key priorities to consider when ensuring overall site safety and safer crushing operations.
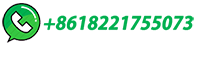
What Is The Crushing Process
Crushing is the process of size reduction of ore. Size reduction process begins with usage of explosives at the area for production of ore. In later stages, the size reduction process performed with crushers before grinding in mills is called "crushing".
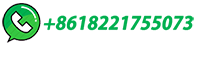
1. Stone Quarrying, Crushing, and Screening Source …
Background Document: General Air Quality Permit for New or Modified Minor Source Stone Quarrying, Crushing, and Screening Facilities in Indian Country ... process rock, sand, gravel, or mineral aggregate or that mines rock, stone, sand and gravel for construction. ... engines at rock crushing facilities which change location …
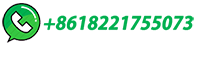
Mining
Rock crushers are used to process material within the mining process chain. Crushers are typically required ahead of conveyors, shafts or other transport or conveying devices. …
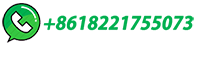
Crushing Plant Flowsheet & Design-Layout
Crushing. To reduce run-of-mine to mill feed requires reduction in a series of stages. The physical size and power requirements of a crusher capable of reducing hard rock vary depending on the application. Extended experience in most crushing plants show that a minus 19MM (¾") rod mill feed can be and is being produced in three stages …
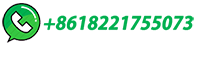
Eco-efficient rock processing
We are shaping eco-efficient rock processing solutions that are driven by a strong collaboration with our customers. With our innovative products and solutions and by u sing digitalization as a key enabler, we ensure that the mining and infrastructure industries have productive, sustainable and cost-effective crushing, screening, breaking and …
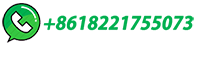